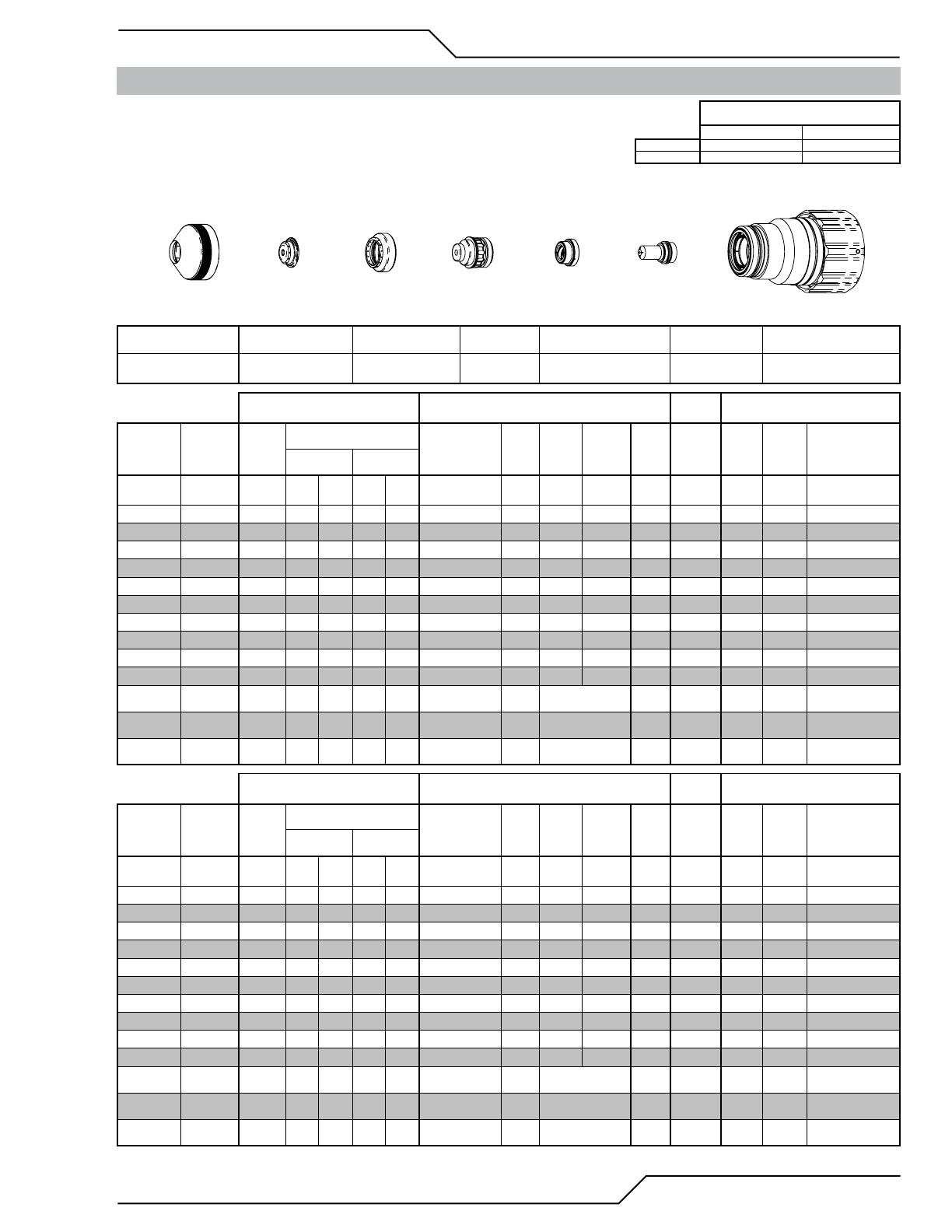
Manaual: 0560956430ES 163 DATOS DE LA ANTORCHA 100i-400i
100i/200i/300i/400i
Acero con bajo contenido de carbono
Caudal de flujo (SLPM/SCFH)
Corte biselado de 200A
O
2
Aire
Preflujo
- / - 162/343
Plasma de O
2
/Protección de aire
Flujo de corte
102/217 133/281
Cartucho
Electrodo
Protección
Distribuidor de
gas de protección
Punta
Distribuidor de
gas de plasma
Copa de
protección
Art # A-07917SP_AC
Utilice esta figura SÓLO para consulta
Retenedor de protección Caperuza protectora
Distribuidor de gas
de protección
Boquilla
Distribuidor de gas
de plasma
Electrodo Cartucho
0559211210 0559210047 0559210073 0559210026 0559210062 0559210005 0559211300
Control manual del gas
Control de altura de la antorcha (THC)
sin altura de elevación
THC
básico
Control CNC
Espesor del
material
efectiva
separación
mínima
Presión de
preflujo
(aire)
Caudal / Presión de corte
Altura de corte
efectiva
Demora
de per
-
foración
THC
Altura de
ignición
de perfo
-
ración
Altura
efectiva
Demora
de con
-
trol
Altura de
perforación
sin eleva
-
ción
Velocidad
de despla
-
zamiento
Demora
de mo
-
vimiento
CNC
Ancho de
sangría máx. a
recomendación de
Velocidad
Plasma (O
2
)
Protección
(aire)
Pulgada (in) (psi) Bola (psi) Bola (psi) (in) (seg) (in) (in) (seg) (in) (ipm) (seg) (in)
0,188 0,080 15 100 100 NA 100 0,130 - 0,550 0,2 0,200 0,150 0,5 0,300 250 0,2 0,142
0,250 0,080 15 100 100 NA 100 0,130 - 0,550 0,2 0,200 0,150 0,5 0,300 200 0,2 0,148
0,375 0,080 15 100 100 NA 100 0,150 - 0,550 0,3 0,250 0,200 0,5 0,350 140 0,3 0,162
0,500 0,080 15 100 100 NA 100 0,170 - 0,550 0,7 0,250 0,200 0,5 0,350 115 0,5 0,167
0,625 0,080 15 100 100 NA 100 0,200 - 0,550 0,9 0,250 0,200 0,5 0,350 80 0,6 0,186
0,750 0,080 15 100 100 NA 100 0,200 - 0,550 1,3 0,300 0,250 0,5 0,400 65 0,8 0,186
0,875 0,080 15 100 100 NA 100 0,200 - 0,550 1,6 0,300 0,250 0,5 0,400 57 1,0 0,185
1000 0,080 15 100 100 NA 100 0,200 - 0,550 1,9 0,300 0,250 0,5 0,400 48 1,2 0,193
1250 0,080 15 100 100 NA 100 0,200 - 0,550 3,2 0,325 0,250 0,5 0,425 30 2,0 0,196
1500 0,080 15 100 100 NA 100 0,200 - 0,550 5,8 0,350 0,300 0,5 0,450 20 4,0 0,201
1750 0,080 15 100 100 NA 100 0,200 - 0,550 1,0
Arranque
desde el borde
0,5 borde 15 1,0 0,203
2000 0,080 15 100 100 NA 100 0,200 - 0,550 1,0
Arranque
desde el borde
0,5 borde 10 1,0 0,204
2500 0,080 15 100 100 NA 100 0,200 - 0,550 1,0
Arranque
desde el borde
0,5 borde 8 1,0 0,210
Control manual del gas
Control de altura de la antorcha (THC)
sin altura de elevación
THC
básico
Control CNC
Espesor del
material
efectiva
separación
mínima
Presión de
preflujo
(aire)
Caudal / Presión de corte
Altura de corte
efectiva
Demora
de per
-
foración
THC
Altura de
ignición
de perfo
-
ración
Altura
efectiva
Demora
de con
-
trol
Altura de
perforación
sin eleva
-
ción
Velocidad
de despla
-
zamiento
Demora
de mo
-
vimiento
CNC
Ancho de
sangría máx. a
recomendación de
Velocidad
Plasma (O
2
)
Protección
(aire)
(mm) (mm) (Bar) Bola (Bar) Bola (Bar) (mm) (seg) (mm) (mm) (seg) (mm)
(mm/
min)
(seg) (mm)
5 2,0 1,0 100 6,9 NA 6,9 3,3 - 14,0 0,2 5,1 3,8 0,5 7, 6 6170 0,2 3,6
6 2,0 1,0 100 6,9 NA 6,9 3,3 - 14,0 0,2 5,1 3,8
0,5 7, 6 5360 0,2 3,7
8 2,0 1,0 100 6,9 NA 6,9 3,6 - 14,0 0,3 5,7 4,5 0,5 8,3 4290 0,3 3,9
10 2,0 1,0 100 6,9 NA 6,9 3,9 - 14,0 0,4 6,4 5,1 0,5 8,9 3460 0,3 4,1
12 2,0 1,0 100 6,9 NA 6,9 4,2 - 14,0 0,6 6,4 5,1 0,5 8,9 3060 0,5 4,2
15 2,0 1,0 100 6,9 NA 6,9 4,9 - 14,0 0,8 6,4 5,1 0,5 8,9 2280 0,6 4,6
20 2,0 1,0 100 6,9 NA 6,9 5,1 - 14,0 1,4 7, 6 6,4 0,5 10,2 1590 0,9 4,7
25 2,0 1,0 100 6,9 NA 6,9 5,1 - 14,0 1,9 7, 6 6,4 0,5 10,2 1250 1,2 4,9
30 2,0 1,0 100 6,9 NA 6,9 5,1 - 14,0 2,8 8,1 6,4 0,5 10,6 890 1,8 5,0
35 2,0 1,0 100 6,9 NA 6,9 5,1 - 14,0 4,5 8,6 7, 0 0,5 11,1 630 3,0 5,0
40 2,0 1,0 100 6,9 NA 6,9 5,1 - 14,0 1,0
Arranque
desde el borde
0,5 borde 470 1,0 5,1
50 2,0 1,0 100 6,9 NA 6,9 5,1 - 14,0 1,0
Arranque
desde el borde
0,5 borde 270 1,0 5,2
60 2,0 1,0 100 6,9 NA 6,9 5,1 - 14,0 1,0
Arranque
desde el borde
0,5 borde 220 1,0 5,3
Los valores en NEGRITA indican los parámetros máximos de perforación. Los valores en NEGRITAS Y CURSIVA solo indican un arranque desde el borde.
8.04 Corte biselado y robótico de 150 - 200 amperios