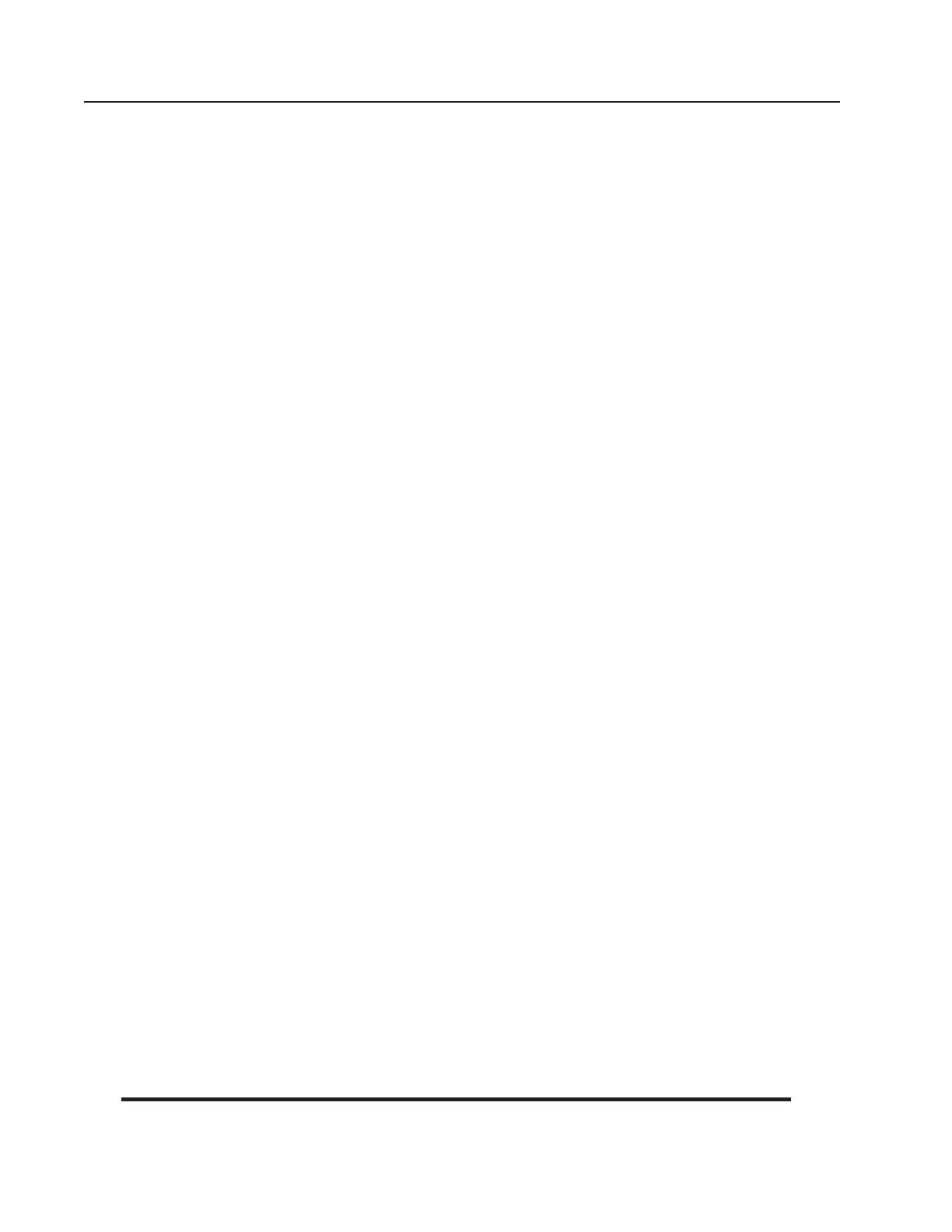
Manual Nro. 0-4800 6-4 PIEZAS Y CONJUNTOS DE REEMPLAZO
Letra clave Descripción Número de catálogo
A,B,C,D,E
Juego de cables de suministro, 3 pies / 1 m (vea la nota 1) 4-3027
A,B,C,D,E Juego de cables de suministro, 10 pies / 3,05 m (vea la nota 1) 4-3028
A,B,C,D,E Juego de cables de suministro, 15 pies / 4,5 m (vea la nota 1) 4-3029
A,B,C,D,E Juego de cables de suministro, 25 pies / 7,6 m (vea la nota 1) 4-3030
A,B,C,D,E Juego de cables de suministro, 35 pies / 10,6 m (vea la nota 1) 4-3050
A,B,C,D,E Juego de cables de suministro, 50 pies / 15,2 m (vea la nota 1) 4-3031
A,B,C,D,E Juego de cables de suministro, 75 pies / 22,9 m (vea la nota 1) 4-3032
A,B,C,D,E Juego de cables de suministro, 100 pies / 30,5 m (vea la nota 1) 4-3033
A,B,C,D,E Juego de cables de suministro, 125 pies / 38,1 m (vea la nota 1) 4-3034
A Cable de retorno de piloto (solo), 4 pies / 1,2 m 9-4890
A Cable de retorno de piloto (solo), 10 pies / 3,05 m 9-4891
A Cable de retorno de piloto (solo), 15 pies / 4.5 m 9-4790
A Cable de retorno de piloto (solo), 25 pies / 7,6 m 9-4791
A Cable de retorno de piloto (solo), 35 pies / 10,6 m 9-9426
A Cable de retorno de piloto (solo), 50 pies / 15,2 m 9-4792
A Cable de retorno de piloto (solo), 75 pies /22,8 m 9-4793
A Cable de retorno de piloto (solo), 100 pies /30,5 m 9-4794
A Cable de retorno de piloto (solo), 125 pies /38,1m 9-4796
B Cable negativo (solo), 3 pies / 1 m 9-4892
B Cable negativo (solo), 10 pies / 3,05 m 9-4897
B Cable negativo (solo), 15’ / 4.5 m 9-4798
B Cable negativo (solo), 25’ / 7,6 m 9-4799
B Cable negativo (solo), 35’ / 10,6 m 9-9427
B Cable negativo (solo), 50’ / 15,2 m 9-4800
B Cable negativo (solo), 75’ / 22,8 m 9-4801
B Cable negativo (solo), 100’ / 30,5 m 9-4802
B Cable negativo (solo), 125’ / 38,1 m 9-4804
C Manguera de suministro de refrigerante (sola), 3 pies / 1 m 9-4886
C Manguera de suministro de refrigerante (sola), 10 pies / 3,05 m 9-4887
C Manguera de suministro de refrigerante (sola), 15 pies / 4,6 m 9-4780
C Manguera de suministro de refrigerante (sola), 20 pies / 6 m 9-4781
C Manguera de suministro de refrigerante (sola), 25 pies / 7,6 m 9-4782
C Manguera de suministro de refrigerante (sola), 30 pies / 9,1 m 9-4783
C Manguera de suministro de refrigerante (sola), 35 pies / 10,6 m 9-4784
C Manguera de suministro de refrigerante (sola), 40 pies / 12 m 9-4785
C Manguera de suministro de refrigerante (sola), 50 pies / 15,2 m 9-4786
C Manguera de suministro de refrigerante (sola), 75 pies / 23 m 9-4787
C Manguera de suministro de refrigerante (sola), 100 pies / 30,5 m 9-4788
D Manguera de suministro de refrigerante (sola), 3 pies / 1 m 9-4888
D Manguera de suministro de refrigerante (sola), 10 pies / 3,05 m 9-4889
D Manguera de suministro de refrigerante (sola), 15 pies / 4,6 m 9-4762
D Manguera de suministro de refrigerante (sola), 20 pies / 6 m 9-4763
D Manguera de suministro de refrigerante (sola), 25 pies / 7,6 m 9-4764
D Manguera de suministro de refrigerante (sola), 30 pies / 9,1 m 9-4765
D Manguera de suministro de refrigerante (sola), 35 pies / 10,6 m 9-4766
D Manguera de suministro de refrigerante (sola), 40 pies / 12 m 9-4767
D Manguera de suministro de refrigerante (sola), 50 pies / 15,2 m 9-4768
D Manguera de suministro de refrigerante (sola), 75 pies / 23 m 9-4769
D Manguera de suministro de refrigerante (sola), 100 pies / 30,5 m 9-4770
NOTA 1:
Los juegos de cables de suministro incluyen el cable de retorno de piloto, el cable negativo, las
mangueras de suministro y retorno de refrigerante y el cable de control.
.