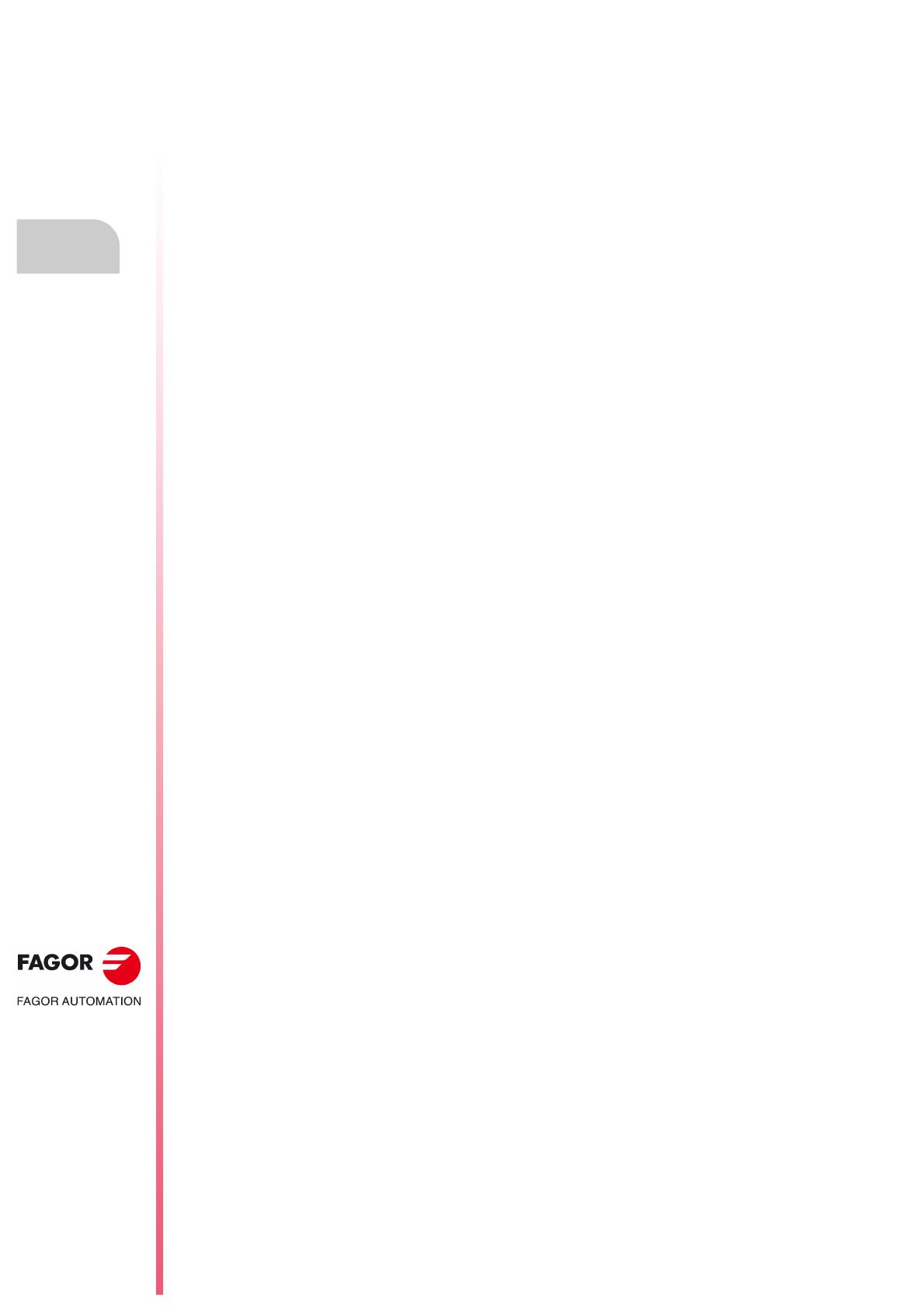
Manual de instalación.
Quercus
CNC 8060
CNC 8065
ꞏ4ꞏ
REF: 2010
2.11.4 Definición de tiempos (sistema)................................................................................. 97
2.11.5 Configuración del bus CAN........................................................................................ 98
2.11.6 Configuración de la línea serie. ................................................................................. 98
2.11.7 Condiciones por defecto (sistema). ........................................................................... 98
2.11.8 Parámetros aritméticos. ............................................................................................. 99
2.11.9 Tablas de compensación volumétrica...................................................................... 101
2.11.10 Tiempos de ejecución. ............................................................................................. 102
2.11.11 Numeración de las entradas digitales (bus CAN). ................................................... 103
2.11.12 Numeración de las salidas digitales (bus CAN)....................................................... 104
2.11.13 Numeración de las entradas analógicas para sondas de temperatura PT100. ....... 105
2.11.14 Configuración del palpador. ..................................................................................... 106
2.11.15 Memoria compartida del PLC. ................................................................................. 108
2.11.16 Gestión de I/O's locales. .......................................................................................... 108
2.11.17 Conmutación sincronizada....................................................................................... 109
2.11.18 PWM (Pulse-Width Modulation)............................................................................... 110
2.11.19 Backup de datos no volátiles. .................................................................................. 111
2.11.20 Offsets y desgaste de las herramientas................................................................... 112
2.11.21 Sincronización de cabezales. .................................................................................. 112
2.11.22 Definir el número de paneles de jog y su relación con los canales. ........................ 113
2.11.23 Renombrar los ejes y cabezales.............................................................................. 113
2.11.24 Traslados de origen. ................................................................................................ 114
2.12 Parámetros máquina generales. Canales de ejecución. ............................................. 115
2.12.1 Configuración del canal. .......................................................................................... 115
2.12.2 Configuración de los ejes del canal. ........................................................................ 116
2.12.3 Configuración de los cabezales del canal................................................................ 119
2.12.4 Configuración del eje C............................................................................................ 120
2.12.5 Definición de tiempos (canal)................................................................................... 121
2.12.6 Configuración del modo HSC (canal). ..................................................................... 122
2.12.7 Eje virtual de la herramienta. ................................................................................... 126
2.12.8 Condiciones por defecto (canal). ............................................................................. 127
2.12.9 Corrección del centro del arco. ................................................................................ 133
2.12.10 Comportamiento del avance y del feed override. .................................................... 134
2.12.11 Override de la dinámica del HSC............................................................................. 135
2.12.12 Movimiento de los ejes independientes. .................................................................. 135
2.12.13 Definición de las subrutinas. .................................................................................... 136
2.12.14 Posición del palpador de sobremesa....................................................................... 138
2.12.15 Búsqueda de bloque. ............................................................................................... 140
2.12.16 Subrutinas de interrupción. ...................................................................................... 140
2.12.17 Avance de mecanizado............................................................................................ 141
2.12.18 Avance rápido para el modo automático. ................................................................ 142
2.12.19 Máxima aceleración y jerk sobre la trayectoria........................................................ 143
2.12.20 Máxima frecuencia sobre la trayectoria. .................................................................. 143
2.12.21 Función retrace. ....................................................................................................... 144
2.12.22 Habilitar la retirada de herramienta en los roscados. .............................................. 145
2.12.23 Cabezal máster........................................................................................................ 145
2.13 Parámetros máquina de los ejes y cabezales. ............................................................ 146
2.13.1 Pertenencia al canal. ............................................................................................... 146
2.13.2 Tipo de eje. .............................................................................................................. 147
2.13.3 Eje Hirth. .................................................................................................................. 147
2.13.4 Configuración de ejes en máquinas tipo torno......................................................... 148
2.13.5 Sincronización de ejes y cabezales. ........................................................................ 149
2.13.6 Configuración de los ejes rotativos. ......................................................................... 150
2.13.7 Configuración del módulo (ejes rotativos y cabezal). .............................................. 152
2.13.8 Configuración del eje C............................................................................................ 152
2.13.9 Configuración del cabezal........................................................................................ 153
2.13.10 Cambio del override del cabezal durante el roscado............................................... 155
2.13.11 Protección antiembalamiento y test de tendencia. .................................................. 156
2.13.12 Offset de PLC. ......................................................................................................... 157
2.13.13 Temporización para ejes muertos............................................................................ 158
2.13.14 Radios / diámetros. .................................................................................................. 159
2.13.15 Búsqueda de referencia........................................................................................... 159
2.13.16 Configuración del movimiento con palpador............................................................ 160
2.13.17 Reposicionamiento de ejes en inspección de herramienta...................................... 161
2.13.18 Configuración de eje independiente. ....................................................................... 161
2.13.19 Configurar el límite máximo de seguridad para el avance y la velocidad. ............... 162
2.13.20 Periodo de muestreo del lazo de posición. .............................................................. 163
2.13.21 Modo de trabajo manual. ......................................................................................... 164
2.13.22 Filtros. ...................................................................................................................... 169
2.13.23 Gamas de trabajo. ................................................................................................... 170
2.14 Parámetros máquina; set de los ejes. ......................................................................... 172
2.14.1 Límites de software de ejes. .................................................................................... 172
2.14.2 Zonas de trabajo. ..................................................................................................... 173
2.14.3 Ajuste del lazo.......................................................................................................... 173
2.14.4 Compensación de holgura con impulso adicional de consigna. .............................. 174
2.14.5 Configurar las captaciones. ..................................................................................... 177