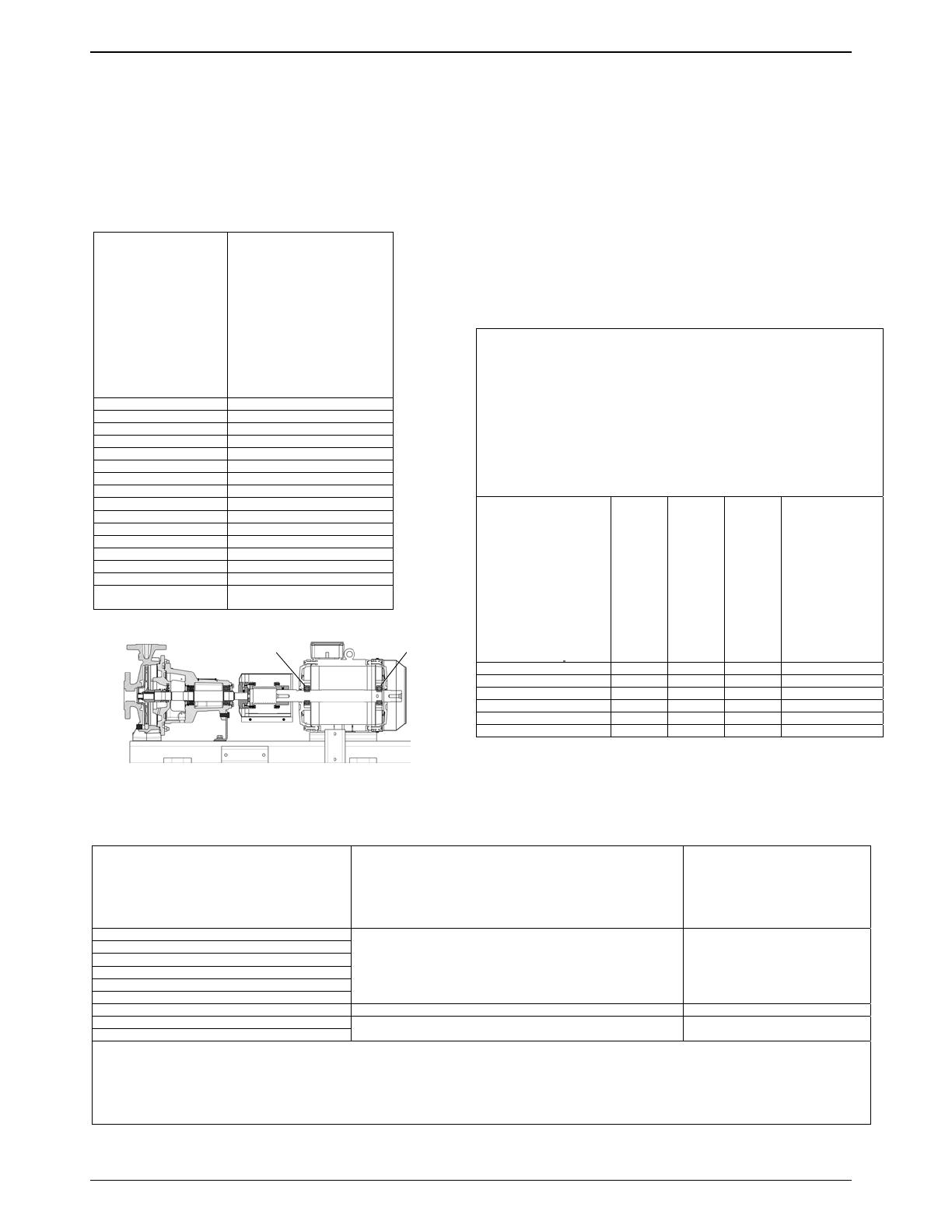
120
TAB.
12.2.1:
Tipo cuscinetto motore pompa KDN STANDARD e pompa KDN OVERSIZ
Type de roulement pour moteur pompe KDN STANDARD et pompe KDN OVERSIZE
Motor bearing type KDN STANDARD pump and KDN OVERSIZE pump
Lagertyp Pumpenmotor KDN STANDARD und Pumpe KDN OVERSIZE
Type motorlager pomp KDN STANDARD en pomp KDN OVERSIZE
Tipo de cojinete motor bomba KDN STANDARD y bomba KDN OVERSIZE
Typ av motorlager för pump KDN STANDARD och pump KDN OVERSIZE
Тип подшипника двигателя насоса KDN STANDARD и насоса KDN OVERSIZE
Tip rulment motor pompa KDN STANDARD şi pompa KDN OVERSIZE
Tipo rolamento motor bomba KDN STANDARD e bomba KDN OVERSIZE
Rodzaj łożyska silnika pompy KDN STANDARD i pompy KDN OVERSIZE
Csapágy típus a KDN STANDARD pumpa motorhoz és a KDN OVERSIZE pumpához
Тип лагер двигател на помпата KDN STANDARD и помпа KDN OVERSIZ
Dimensioni del motore
Dimensions du moteur
Motor size
Abmessungen des Motors
Afmetingen van de motor
Dimensiones del motor
Mått på motor
Габариты двигателя
Dimensiuni motor
Dimensões do motor
Wielkość silnika
A motor méretei
Размери на двигателя
ﻙﺮﺤﻤﻟﺍ ﺩﺎﻌﺑﺃ
Tipo di cuscinetto
Pompe KDN
Type de roulement - Pompes KDN
Bearing type – Pumps KDN/Lagerart
Pumpen KDN/Lagertype – Pompen KDN
Tipo de cojinete – Bombas KDN
Typ av lager – Pumpar KDN
Тип подшипника – Насосы KDN
Tip de rulment – Pompe KDN
Tipo de rolamento – Bombas KDN
Rodzaj łożyska – Pompy KDN
Csapágy típus – KDN pumpa
Тип лагер - KDN помпи
MEC 63 6201-2Z
MEC 71 6203-2Z
MEC 80 6204-2Z
MEC 90 6205-2Z
MEC 100 6206-2Z
MEC 112 6306-2Z
MEC 132 6208-2Z
MEC 160 6309-2Z
MEC 180 6311-C3
MEC 200 6312 C3
MEC 225 6313 C3
MEC 250 6314 C3
MEC 280 6316 C3
MEC 280 6316 C3
MEC 315 2P 6317 C3
MEC 315 4P-8P
DE= NU319
NDE= 6319 C3
Lubrificazione permanente fino a MEC 160/Lubrification permanente jusqu’à MEC 160
Permanent lubrication up to MEC 160/Permanente Schmierung bis MEC 160
Permanente smering tot MEC 160/Lubricación permanente hasta MEC 160
Permanentsmörjning upp till MEC 160/Перманентная смазка до MEC 160
Lubrifiere permanentă până la MEC 160/
Lubrificação permanente até MEC 160.
Stałe smarowanie, aż do MEC 160/MEC 160-ig érvényes, örökös kenőzsírozás
Постоянно смазване до MEC 160/ MEC 160 ﺔﻤﺋﺍﺩ ﻢﻴﺤﺸﺗ ﺓﺩﺎﻣﻰﻟﺇ
Da MEC 180 lubrificanti M10x1 DIN 3404 (vedi tabella sotto)
À partir de MEC 180 lubrifiants M10x1 DIN 3404 (voir le tableau ci-dessous)
From MEC 180 greasers M10x1 DIN 3404 (see table below)
Von MEC 180 Schmiermittel M10x1 DIN 3404 (siehe unten stehende Tabelle)
Vanaf MEC 180, smeermiddelen M10x1 DIN 3404 (zie tabel hieronder)
De MEC 180 lubricantes M10x1 DIN 3404 (ver tabla siguiente)
Från MEC 180, smörjnipplar M10x1 DIN 3404 (se tabell nedan)
От MEC 180 масленки M10x1 DIN 3404 (см.таблицу ниже)
De la MEC 180 lubrifianți M10x1 DIN 3404 (vezi tabelul de mai jos)
De MEC 180 lubrificantes M10x1 DIN 3404 (ver tabela abaixo)
Od MEC 180 smarowane M10x1 DIN 3404 (patrz tabela poniżej)
MEC 180 felett használható kenőzsírok M10x1 DIN 3404 (lásd az alábbi táblázatban)
От MEC 180 смазочни материали M10x1 DIN 3404 (вижте таблицата по-долу)
INTERVALLO DI LUBRIFICAZIONE per temperature di servizio fino a 70° (ore di servizio)
PLAGE DE LUBRIFICATION pour températures de service jusqu'à 70 ° (heures de service)
GREASING INTERVAL for operating temperature up to 70°C (operating hours)
SCHMIERINTERVALL für Betriebstemperaturen bis 70° (Betriebsstunden)
SMEERINTERVAL voor bedrijfstemperaturen tot 70° (bedrijfsuren)
INTERVALO DE LUBRICACIÓN para temperaturas de servicio de hasta 70° (horas de servicio)
SMÖRJINTERVALL för driftstemperaturer upp till 70 °C (driftstimmar)
ПЕРИОДИЧНОСТЬ СМАЗКИ при рабочей температуре до 70° (часов работы)
INTERVAL DE LUBRIFIERE pentru temperaturi de serviciu de până la 70 ° (ore de serviciu)
INTERVALO DE LUBRIFICAÇÃO para temperaturas de serviço até 70° (horas de serviço)
PRZERWA W SMAROWANIU dla temperatury pracy, aż do 70° (godziny pracy)
KENŐZSÍROZÁSI SZÜNET, a 70° fokot meghaladó munkavégzési hőmérsékleten (munkavégzési órák)
ВРЕМЕВИ ИНТЕРВАЛИ МЕЖДУ ГРЕСИРАНИЯТА за работни температури до 70 ° (работни часове)
ﻰﺘﺣ ﻞﻴﻐﺸﺘﻟﺍ ﺓﺭﺍﺮﺣ ﺕﺎﺟﺭﺩ ﻲﻓ ﻢﻴﺤﺸﺘﻟﺍ ﺓﺭﻭﺩ70 (ﺔﻣﺪﺨﻟﺍ ﺕﺎﻋﺎﺳ) ﺔﻳﻮﺌﻣ ﺔﺟﺭﺩ
DIMENSIONI DEL MOTORE
DIMENSIONS DU MOTEUR
MOTOR SIZE
ABMESSUNGEN DES MOTORS
AFMETINGEN VAN DE MOTOR
DIMENSIONES DEL MOTOR
MÅTT PÅ MOTOR
ГАБАРИТЫ ДВИГАТЕЛЯ
DIMENSIUNI MOTOR
DIMENSÕES DO MOTOR
WIELKOŚĆ SILNIKA
A MOTOR MÉRETEI
РАЗМЕРИ НА ДВИГАТЕЛЯ
ﻙﺮﺤﻤﻟﺍ ﺩﺎﻌﺑﺃ
3000 RPM 1500 RPM 1000 RPM
Quantità gr./Quantité gr.
Quantity gr./Menge in g.
Hoeveelheid gr.
Cantidad g./Fettmängd
Количество в г
Cantitate gr.
Quantidade gr.
Ilość g.
Gramm mennyiség
Количество гр
ﺕﺎﻣﺍﺮﺠﻟﺎﺑ ﺔﻴﻤﻜﻟﺍ
MEC 180 4000 9000 1300 15
MEC 200 3500 8000 1200 20
MEC 225 3000 7500 1100 23
MEC 250 2000 7000 1000 26
MEC 280 1500 6500 900 40
MEC 315 1000 4000 800 55
TAB.
12.2.2:
Tipo di cuscinetti lato bagnato STD KDN/Type de roulements côté humide STD KDN /Bearing type wet end STD KDN/Lagerart nasse Seite STD KDN/Type lagers natte zijde STD
KDN/Tipo de cojinetes lado mojado STD KDN/Typ av lager på den våta sidan STD KDN/Тип подшипников с увлажненной стороны STD KDN/Tip de rulmenţi partea umedă STD
KDN/Tipo de rolamentos lado molhado STD KDN/Rodzaj łożyska po stronie mokrej STD KDN/Csapágy típus nedves részen STD KDN/Тип лагери STD KDN от мократа страна
STD KDN ﻉﻮﻧﺕﺎﻴﺸﺣ ﻞﺘﺒﻤﻟﺍ ﺐﻧﺎﺠﻠﻟ ﻙﺎﻜﺘﺣﻻﺍ ﻊﻨﻣ
Modello/Modèle/Model/Modell/Model/Modelo/Modell/Модель
Model/Modelo/Model/Modell/Модел/ﻝﻳﺩﻭﻣﻟﺍ
Tipo di supporto Ø albero idraulico/Type de support Ø arbre hydraulique
Type of support Ø hydraulic shaft/Lagerart Ø Hydraulikwelle
Type steun Ø hydraulische as/Tipo de soporte Ø eje hidráulico
Typ av stöd Ø hydraulaxel/Тип опоры Ø гидравлического вала
Tip de suport Ø arbore hidraulic/Tipo de suporte Ø veio hidráulico
Rodzaj podpory Ø wału hydraulicznego/Ø hidraulikus tengely támaszték típusa
Тип опора Ø на хидравличния вал/
ﻲﻜﻴﻟﻭﺭﺪﻴﻬﻟﺍ ﺩﻮﻤﻌﻟﺍ Ø ﺔﻣﺎﻋﺩ ﻉﻮﻧ
Tipo di cuscinetto/Type de roulement/Bearing
Type/Lagerart/Lagertype
Tipo de cojinete/Typ av lager
Тип подшипника/Tip de rulment
Tipo de rolamento/Rodzaj łożyska
Csapágy típus/Тип лагер
ﻉﻮﻧﺔﻴﺸﺣ ﻙﺎﻜﺘﺣﻻﺍ ﻊﻨﻣ
KDN 32-125.1 - KDN 32-125 - KDN 32-160.1 - KDN 32-160
24 6306 ZZC3
KDN 32-200.1 - KDN 32-200
KDN 40-125 - KDN 40-160 - KDN 40-200 - KDN 40-250
KDN 50-125 - KDN 50-160 - KDN 50-200 - KDN 50-250
KDN 65-125 - KDN 65-160 - KDN 65-200 - KDN 65-250
KDN 65-315
KDN 80-160- KDN 80-200- KDN 80-250- KDN 80-315 24 6306 ZZC3
KDN 100-200- KDN 100-250- KDN 100-315
32 6308 2Z C3
KDN 125-250- KDN 150-200
- cuscinetti ingrassati a vita e comunque ogni 3 anni o 20.000 ore/roulements graissés à vie et en tous les cas tous les 3 ans ou toutes les 20.000 heures
- bearings greased for life and at least every 3 years or 20,000 hours/dauerhaft gefettete Lager und auf jeden Falle alle 3 Jahre oder 20.000 Stunden
- lagers gesmeerd voor de levensduur en hoe dan ook elke 3 jaar of 20.000 uur/cojinetes engrasados de por vida y, en todo caso, cada 3 años o 20.000 horas
- livstidssmorda lager och oavsett vart 3:e år eller var 20 000:e driftstimme/подшипники смазаны пожизненно: они нуждаются в смазке раз в 3 года или каждые 20 000 часов работы
- rulmenți unşi pe viaţă şi oricum la fiecare 3 ani sau 20.000 ore/rolamentos de lubrificação permanente e de qualquer modo em cada 3 anos ou 20.000 horas
- łożyska smarowane na cały okres eksploatacja, zawsze co 3 lata lub 20.000 godzin/örökre zsírozott csapágyak, minden esetre 3 év vagy 20.000 óra érvénnyel
- лагери смазани за цял живот и във всеки случай на всеки 3 години или на 20 000 часа/
ﺕﺎﻴﺸﺣ ﻞﻛ ﻝﺎﺣ ﻱﺃ ﻰﻠﻋﻭ ﺓﺎﻴﺤﻟﺍ ﻯﺪﻣ ﺔﻤﺤﺸ
ُ
ﻣ ﻙﺎﻜﺘﺣﺍ ﻊﻨﻣ3 ﻭﺃ ﺕﺍﻮﻨﺳ20.000 .ﺔﻋﺎﺳ
ﻉﻮﻧﺔﻴﺸﺣ ﻟ ﻙﺎﻜﺘﺣﻻﺍ ﻊﻨﻣ ﻙﺮﺤﻤ ﺔﺨﻀﻣKDN STANDARD ﺔﺨﻀﻣﻭKDN OVERSIZE
ﻦﻣMEC 180 ﻢﻴﺤﺸﺗ ﺩﺍﻮﻣM10×1 DIN 3404 (ﻩﺎﻧﺩﺃ ﻝﻭﺪﺠﻟﺍ ﺮﻈﻧﺍ)
ﻉﻮﻧﺔﻴﺸﺣ ﻙﺎﻜﺘﺣﻻﺍ ﻊﻨﻣ- ﺕﺎﺨﻀﻤﻟﺍKDN
DE
NDE