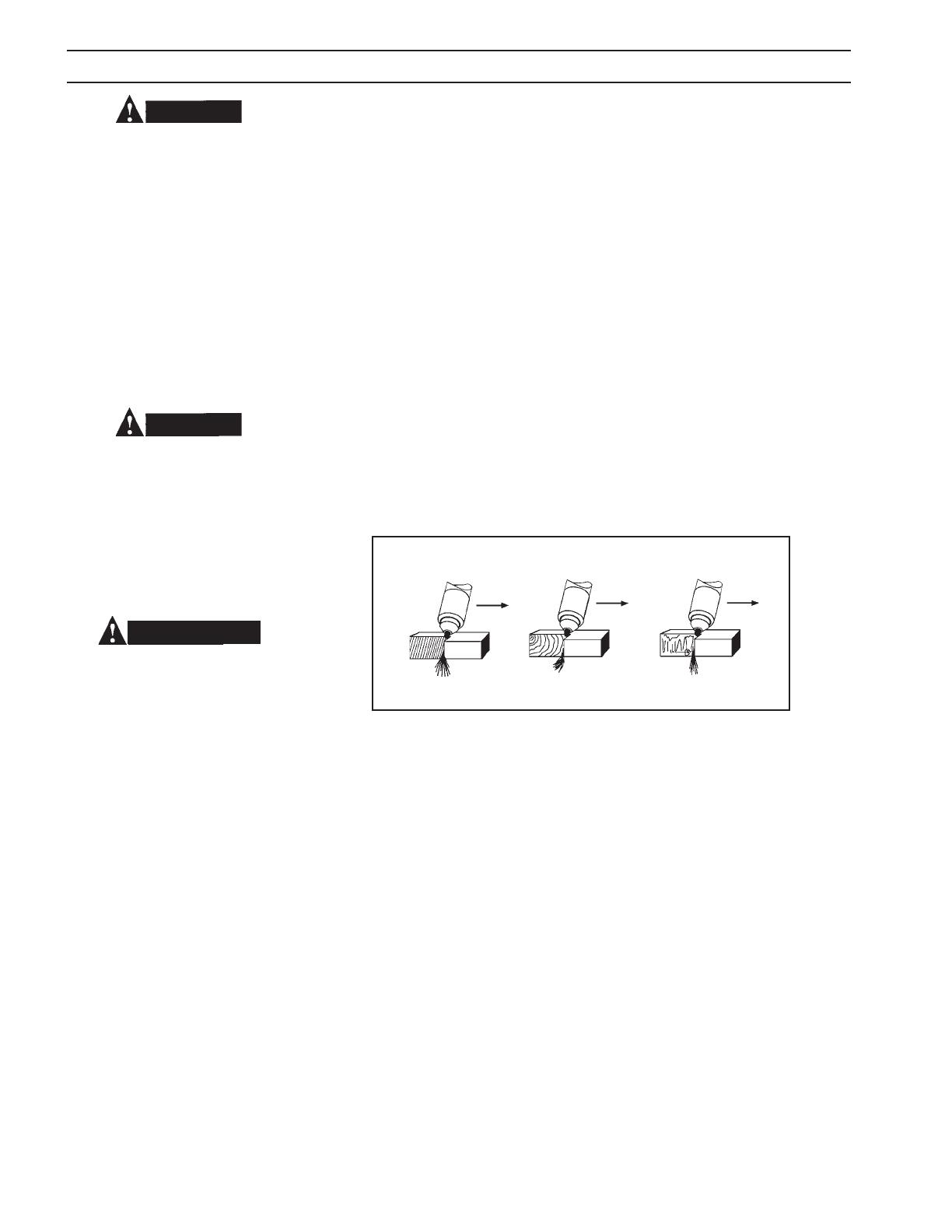
156
AVVISO
Con un angolo di taglio positivo, le dimensioni della parte in alto saranno legger-
mente inferiori a quelle della parte in basso. Con un angolo di taglio negativo, le
dimensioni della parte in alto saranno leggermente superiori a quelle della parte
in basso. L’angolo di taglio viene controllato dallo stand-o (tensione d’arco), dalla
velocità di taglio e dalla corrente di taglio. Se la velocità e la corrente di taglio sono
quelle corrette e la parte presenta un angolo positivo eccessivo, lo stand-o è troppo
elevato. Iniziare ad abbassare la tensione d’arco con incrementi di 5 volt, rispettando
la quadratura del taglio. Se si usa l’azoto, esisterà sempre un leggero arrotondamento
del bordo superiore.
L’altezza ottimale della torcia è il punto che precede appena il momento in cui la
parte inizia a sviluppare un angolo di taglio negativo. Per entrare nei dettagli delle
altre due variabili, con uno stando adeguato, l’eccessiva velocità di taglio avrà come
risultato un angolo di taglio positivo, mentre una velocità insuciente genererà un
angolo di taglio negativo. In caso di corrente di taglio troppo alta o troppo bassa, il
risultato sarà un angolo di taglio positivo.
Tensione d’arco/Stando - Parametri interattivi proporzionali. Una posizione più
elevata della torcia rispetto alla piastra richiederà una maggior tensione d’esercizio
e viceversa.
Linee sfasate - Appaiono sulla supercie di taglio ed aiutano a determinare la cor-
rettezza dei parametri di processo.
I RAGGI DELL’ARCO POSSONO CAUSARE
USTIONI AGLI OCCHI E ALLA PELLE,
MENTRE IL RUMORE POTREBBE
DANNEGGIARE L’UDITO.
Indossare protezioni per occhi, orecchie
e corpo.
Indossare guanti, indumenti ed elmetto
protettivi. Un elmetto con ltro lenti N. 6
o 7 dovrebbe orire protezione adeguata
per gli occhi.
Non toccare mai le parti anteriori
all’impugnatura della torcia (ugello,
scudo termico, elettrodo, ecc.) a meno che
l’intettuttore Power si trovi in posizione
OFF.
NON accendere l’unità quando la
copertura viene rimossa.
NON applicare la corrente all’unità
mentre la si trattiene o la si trasporta.
NON toccare alcuna parte della torcia
quando l’interruttore si trova nella
posizione “on”.
Posizionare l’ESP-150 ad almeno 3 metri
dall’area di taglio. Scintille e scorie calde
risultanti dalle operazioni di taglio
possono danneggiare l’unità.
velocità
corretta
troppo
lenta
troppo
veloce
Fig. 8 - Eetto della velocit
à di taglio
NOTA: sel’arcoditagliononsiattivaentro6secondi,l’arcopilotasispegnerà
Smetteredipremerel’interruttoredellatorcia.Controllarechelepressionidei
gassianoadeguate,cheilcavosiasaldamentecollegatoalpezzodalavorare,
chelatorciasiasollevataadun’altezzadi3,1-6,3mm(1/8-1/4”)dalpezzoda
lavorare,ecc.Quindi,ricominciaredalpassaggio1.
4. Per il taglio manuale e meccanizzato, mantenere uno stand-o (distanza tem-
poranea torcia-pezzo) di circa 9,5 mm (la guida di stand-o, N° parte 36648,
fornisce questa distanza). Mantenere verticale la punta della torcia, e muoverla
ad una velocità tale da produrre la desiderata qualità di taglio. Il taglio dovrebbe
produrre uno spruzzo diretto di piccole particelle di metallo fuso sotto il pezzo
da lavorare, come illustrato nella Fig. 8. Per il taglio meccanizzato, fare riferimento
alla tabella 2 o 3 per la gamma di velocità di taglio consigliate.
5. Se l’arco di taglio si perde durante la fase di taglio, l’arco pilota si riaccenderà
immediatamente, se si mantiene premuto l’interruttore della torcia. L’operatore
ha circa 6 secondi a disposizione per portare la torcia abbastanza vicina al pezzo
e ripristinare l’arco di taglio.
6. L’arco di taglio si estinguerà alla ne dell’operazione di taglio; in ogni caso,
l’interruttore della torcia non deve restare premuto al ne di impedire la riaccen-
sione dell’arco pilota.
7. Una volta ultimata l’operazione di taglio, attendere qualche minuto prima di
portare l’interruttore POWER in posizione OFF per dare tempo al ventilarore di
rareddare l’unità. Quindi, spegnere l’interruttore principale.
AVVISO
ATTENZIONE
SEZIONE 4 FUNZIONAMENTO