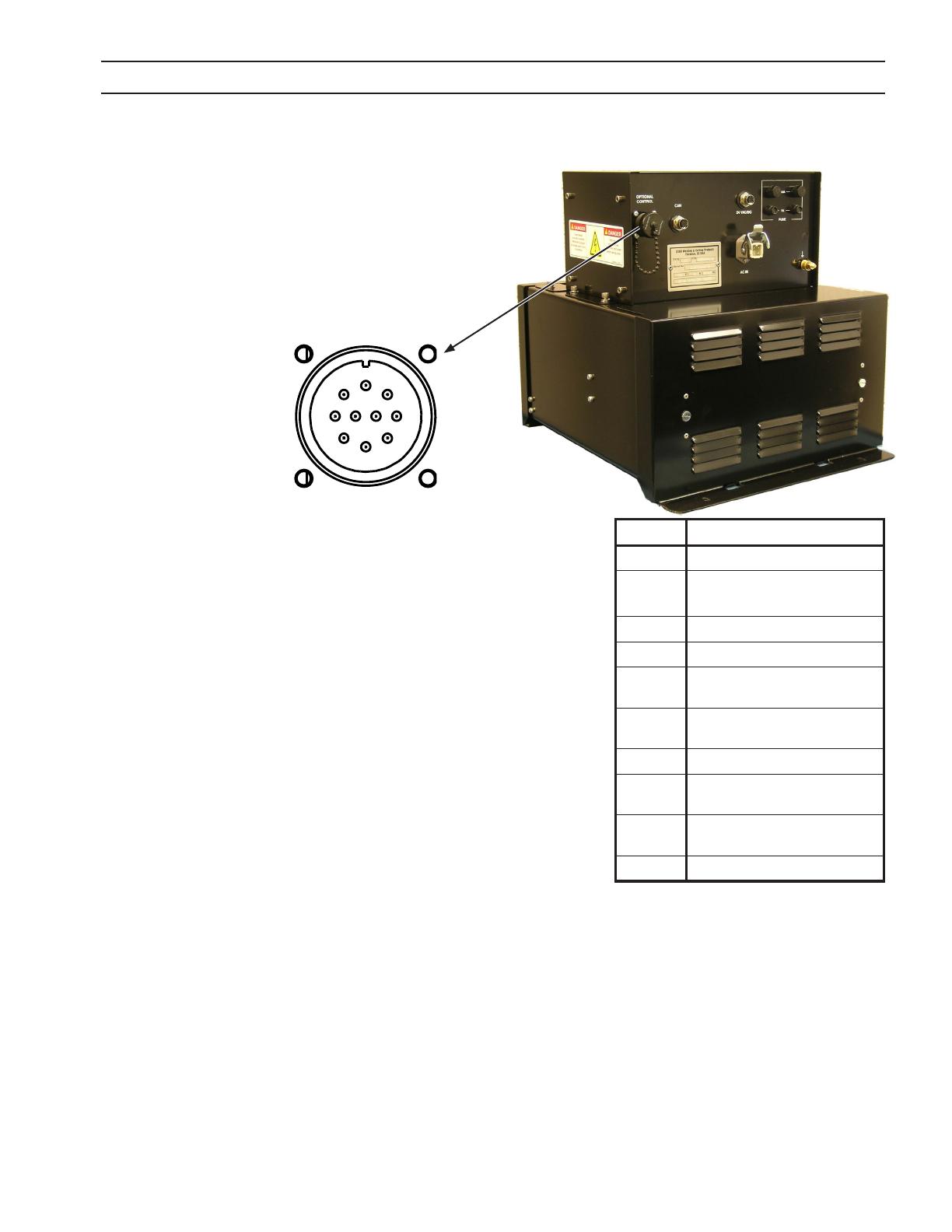
17
SECCIÓN 4 FUNCIONAMIENTO
4.2 Funcionamiento en el modo
de Control opcional
Cuando las comunicaciones CAN no están disponibles,
el WIC puede trabajar en el modo de Control
opcional. Esto ocurre cuando se retroalimenta un
sistema más viejo con el soplete PT-36. En este modo,
todos los comandos vienen del conector externo de
10 clavijas etiquetado “CONTROL OPCIONAL” en el
panel posterior del WIC. A continuación se enumeran
las señales de este conector de 10 clavijas:
CLAVIJA
Función
A +24VCC (SALIDA)
B
Anticongelamiento ex-
terno
C CNC COM
D Fallo
E
COM de referencia
externa
F
Referencia de ujo
externo
G Salida del ujo de agua
H
Salida de la presión
de agua
J
+24VCC
(desde la clavija A)
K Armazón
La clavija A (+24VCC) es una salida hacia el cliente. El cliente debe
enviar +24 VCC a través de la clavija B para activar la función de
anticongelamiento. La clavija D es la señal de fallo, que es normalmente
alta y el nivel de la señal viene de la clavija C. En caso de fallo, la clavija
D se restablecerá a bajo. El cliente debe controlar la clavija D en busca
de fallos. El ujo del agua se proporciona al sistema mediante la clavija
E y la clavija F. Cada voltio proporciona 0.2gpm, por ejemplo: 5V =
>1.0gpm o 1V = >0.2gpm. El sistema también puede proporcionar el
ujo del agua y la presión del agua al cliente. Para estas dos señales,
las relaciones de representación son: 5V = >1gpm para el ujo, 5V =
>100psi (6.9bar) para la presión.
Las salidas de la clavija D (fallo), la clavija G (salida del ujo del agua) y
la clavija H (salida de la presión del agua) están disponibles tanto en el
modo de Comunicación CAN como en el modo de Control opcional.
Para arrancar la bomba, se necesita un comando de ujo de agua.
El ujo mínimo es de 0.15gpm. En el caso del modo de Control opcional,
cada voltio ordenará un ujo de agua de 0.2gpm. Sin embargo, el comando de ujo debe cumplir con el requi-
sito mínimo. Si hay un comando de ujo de agua disponible desde CAN y es mayor que el requisito mínimo de
ujo, el WIC ignorará el comando del ujo del agua del conector de 10 clavijas.
Mientras la bomba está en funcionamiento, el ujo de agua y la presión del agua reales siempre están disponibles
desde el conector de 10 clavijas. El cliente puede usarlos para resolver problemas.
4.3 Precaución con el motor
La bomba utilizada en esta aplicación tiene una derivación regulable para mantener la presión en un determinado
nivel. Con las conguraciones de fábrica, la bomba puede aumentar la presión a un nivel de 150psi (10.4bar)
por encima de la presión de entrada. Si se la deja funcionar continuamente y se interrumpe el ujo, el calor del
motor puede aumentar la temperatura del agua a un nivel alto. Esto producirá un calor excesivo que hará que
el motor falle.
DISPOSICIÓN
DE LA CLAVIJA DE
CONTROL
OPCIONAL
VISTA EXTERIOR
A
B
C
D
E
F
G
H
J
K
Para el modo de Control opcional, se deben puentear la clavija A y la
clavija J para proporcionar 24VCC al PCUA.