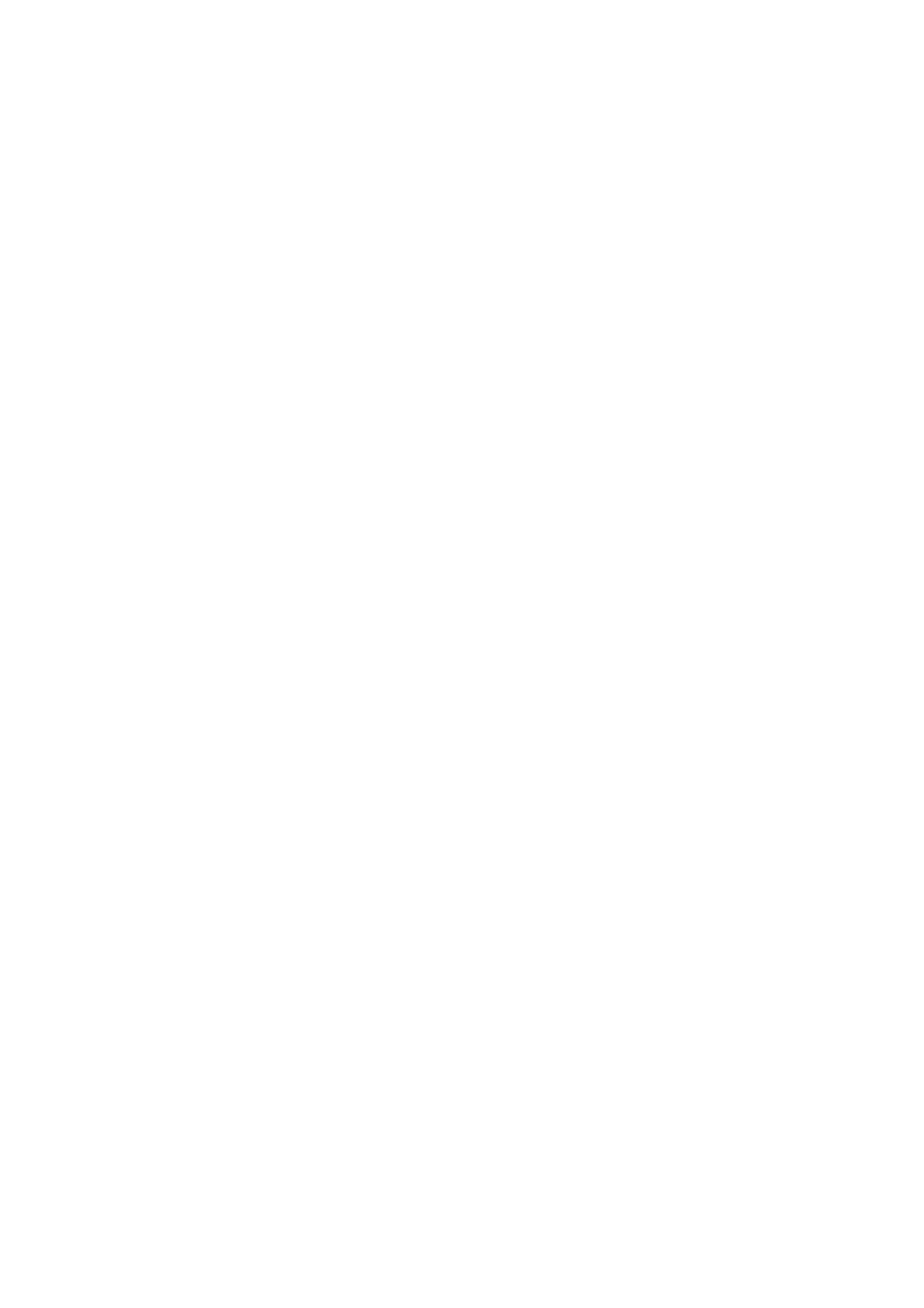
P31 T1. Tiempo entre freno y consigna o señal rápido (en mseg).................................Apartado 4.5
P32 T2. Tiempo entre Banda de Muerte y freno del eje X (en mseg) ............................Apartado 4.5
P33 T3. Tiempo entre freno y señal en Posición del eje X (en mseg)............................Apartado 4.5
P34 T4. Duración de la señal en Posición del eje X (en mseg) ......................................Apartado 4.5
P35 Modo de operación activo tras encendido (si <900 Auto, si >899 Manual) ..........Apartado 3.3
P36 Máxima velocidad del cabezal en la GAMA 1 ......................................................Apartado 5.1
P37 Máxima velocidad del cabezal en la GAMA 2 ......................................................Apartado 5.1
P38 Máxima velocidad del cabezal en la GAMA 3 ......................................................Apartado 5.1
P39 Máxima velocidad del cabezal en la GAMA 4 ......................................................Apartado 5.1
P40 Límite de recorrido positivo del eje Y....................................................................Apartado 4.7
P41 Límite de recorrido negativo del eje Y...................................................................Apartado 4.7
P42 Cota de referencia máquina del eje Y.....................................................................Apartado 4.6
P43 Distancia de frenado del eje Y (lazo abierto) .........................................................Apartado 4.4
P44 a P48 Sin función
P49 Resolución de contaje del eje Y (en micras) ..........................................................Apartado 4.1
P50 Ganancia proporcional K1 del eje Y ......................................................................Apartado 4.4
P51 Ganancia proporcional K2 del eje Y ......................................................................Apartado 4.4
P52 Sin función
P53 Consigna mínima del eje Y (1=2,5mV) ..................................................................Apartado 4.2
P54 Holgura del husillo en el eje Y (impulsos de contaje) ...........................................Apartado 4.8
P55 Impulso adicional de consigna del eje Y (1=2,5mV) .............................................Apartado 4.8
P56 Nodo que ocupa el CNC o número de nodos en la red...........................................Apartado 5.3
P57 Registro del PLC64 al que se envían las funciones M, S, T ...................................Apartado 5.3
P58 Número de nodo al que se envían las funciones M, S, T ........................................Apartado 5.3
P59 (8) Bits de parada (0=1, 1=2)........................................................................................Apartado 5.2
(7) Número de bits de información por carácter (0=7, 1=8) .........................................Apartado 5.2
(6) Paridad par (0=No, 1=Si) ........................................................................................Apartado 5.2
(5) Paridad (0=No, 1=Si) ..............................................................................................Apartado 5.2
(4) El CNC ocupa el nodo principal de la red local (0=No, 1=Si) ...............................Apartado 5.3
(3) Tipo de señal de captación del eje Y (0=Cuadrada, 1=Senoidal)...........................Apartado 4.1
(2) Tipo de señal de captación del eje X (0=Cuadrada, 1=Senoidal)...........................Apartado 4.1
(1) Red local Fagor (0=No, 1=Si) .................................................................................Apartado 5.3
P60 (8) La máquina dispone de eje Y (0=Si, 1=No) ............................................................Apartado 3.4
(7) Los valores de K1 y K2 son en mv/ impulso. Eje Y (0=No, 1=Si) ..........................Apartado 4.4
(6) Los valores de K1 y K2 son en mv/ impulso. Eje X (0=No, 1=Si) ..........................Apartado 4.4
(5) Tabla de herramientas (0) o tabla de traslados de origen (1) ..................................Apartado 3.3
(4) La máquina dispone de volante electrónico (0=No, 1=Si) .....................................Apartado 3.4
(3) Salida S en BCD de 2 o 4 dígitos (0=2, 1=4)..........................................................Apartado 5.1
(2) Salida S analógica (0) o en BCD (1) .......................................................................Apartado 5.1
(1) G00 vectorizado (0=No, 1=Si)................................................................................Apartado 3.8
P61 (8) El eje X es un eje visualizador (0=No, 1=Si) .........................................................Apartado 3.4
(7) El eje Y es un eje visualizador (0=No, 1=Si) .........................................................Apartado 3.4
(6) Factor multiplicador de las señales del eje Y (0=x4, 1=x2) ...................................Apartado 4.1
(5) La función T genera salida BCD (0=Si, 1=No).......................................................Apartado 3.5
(4) Búsqueda de referencia máquina tras el encendido (0=No, 1=Si) ..........................Apartado 4.6
(3) Orden de desplazamiento de los ejes con la función G74 (0=1º X, 1=1º Y)...........Apartado 4.6
(2) Eje Y rotativo HIRTH (0=No, 1=Si) .......................................................................Apartado 3.4
(1) Eje Y rotativo ROLLOVER por el camino más corto (0=No, 1=Si) .......................Apartado 3.4
P62 (8) Micro de referencia máquina del eje Y (0=No, 1=Si) .............................................Apartado 4.6
(7) Alarma de captación activa (0) o inactiva (1) en el eje Y.......................................Apartado 3.5
(6) Eje Y rotativo ROLLOVER (0=No, 1=Si)...............................................................Apartado 3.4
(5) Sentido búsqueda referencia máquina del eje Y (0=Positivo, 1=Negativo)...........Apartado 4.6
(4) Sentido búsqueda referencia máquina del eje X (0=Positivo, 1=Negativo)...........Apartado 4.6
(3) Resolución de 0,0001 milímetros (0,00001 pulgadas) (0=No, 1=Si) .....................Apartado 4.9
(2) Sentido de contaje del eje Y ..................................................................................Apartado 4.
(1) Signo de la consigna del eje Y...............................................................................Apartado 4.
P63 (8) Signo factor corrección de captación del eje X (0=Positivo, 1=Negativo) ............Apartado 4.1
(7) Signo factor corrección de captación del eje Y (0=Positivo, 1=Negativo) ............Apartado 4.1
(6) Tipo de impulso del palpador de medida (0=Negativo, 1=Positivo) .....................Apartado 3.5
(5) Tipo de impulso de referencia máquina del eje Y (0=Negativo, 1=Positivo) ........Apartado 4.6
(4) Eje X en radios (0) o diámetros (1) .........................................................................Apartado 3.3
(3) La máquina dispone de roscado rígido (0=No, 1=Si) .............................................Apartado 3.4
(2) Sentido de desplazamiento en modo MANUAL del eje Y ....................................Apartado 4.
(1) Aceleración/deceler. en todos los desplazamientos en G01 (0=No, 1=Si) .............Apartado 4.4
P64 Avance en los modos MANUAL y PLAY-BACK del eje Y ...................................Apartado 4.3
P65 Avance en la búsqueda de referencia máquina del eje Y .......................................Apartado 4.6