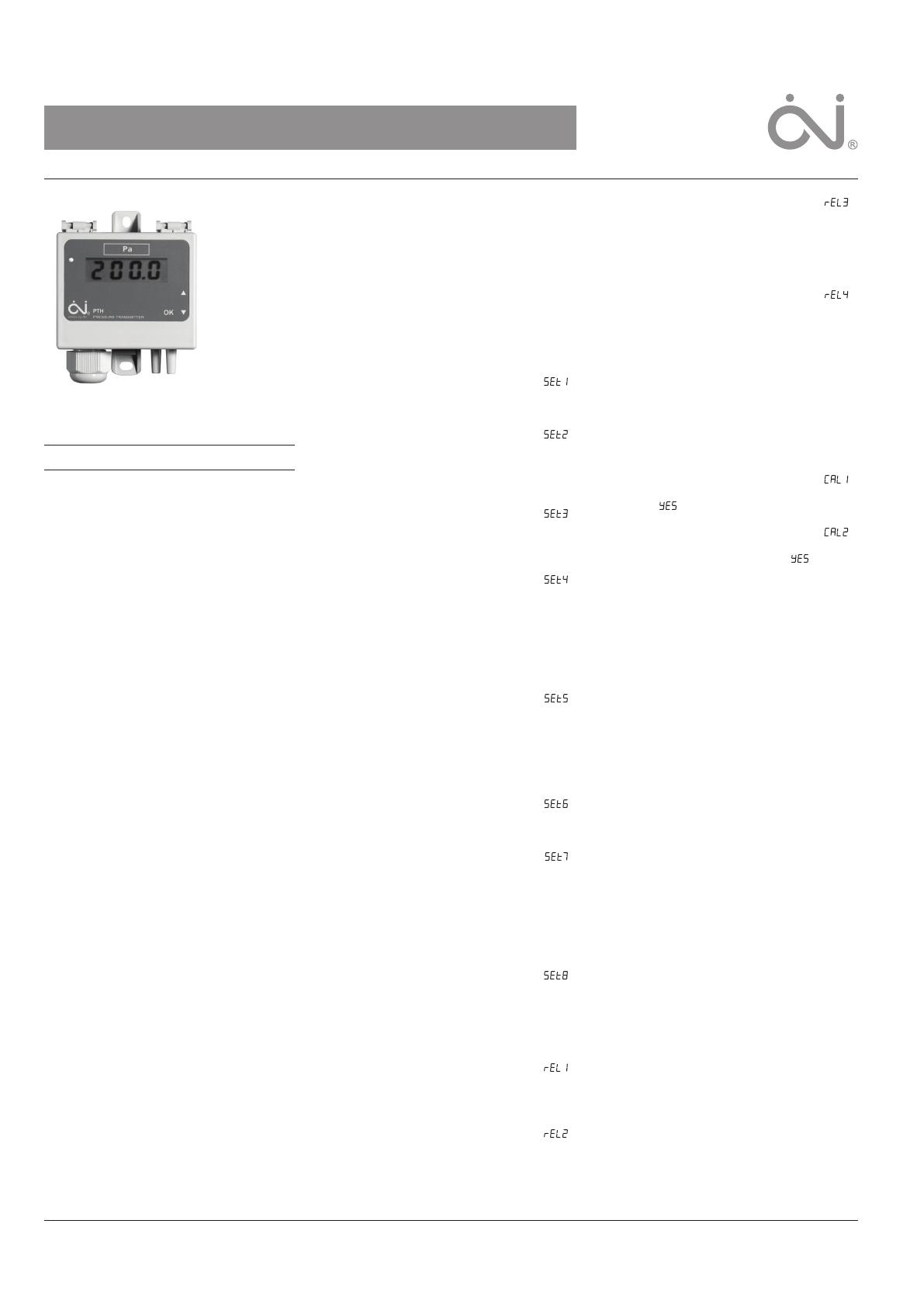
INSTRUCTIONS
© 2020 OJ Electronics A/S
67642B 05/20 - (PBV)
PTH-3202-DR
• English
• Español
English
LIST OF FIGURES
The following figures are located at the back of
the instructions:
Fig. 1: Menu scheme
Fig. 2: Dimensioned drawing
Fig. 3: Position of transmitter in relation to
bends and branches
Fig. 4: Wiring diagram
Fig. 5:
Relay operation diagram
Fig. 6: Orientation of PTH
INTRODUCTION
PTH-3202-DR is electronic air pressure / flow
transmitter with integrated relay. The relay can
be used as feedback to a BMS system or to
control an audio/visual alarm. PTH has an 0-10V
and 0-20mA analog output for read-out of air
pressure / flow.
PTH use a semiconductor pressure element
with no air throughput, thus protecting the
unit from dust in the ventilation system. The
pressure element is temperature compensated
to provide accurate pressure measurement
throughout the specified temperature range.
See ‘Technical Data’.
INSTALLATION
PTH should be attached to a firm, level surface
using two screws. The pressure controller also
functions with only one tube fitted to the tube
connectors (+ or -). However, two tubes should
always be fitted to maintain the enclosure rat-
ing.
Pressure is supplied to the measurement unit by
tubes, the higher pressure being connected to
the ‘+ tube connector’ and the lower pressure
to the ‘÷ tube connector’ (see fig. 4).
The pressure tubes must be as short as pos-
sible and must be secured in position to prevent
vibration.
To obtain the best possible results, pressure
must be measured where there is least risk of
turbulence, i.e. in the centre of the ventilation
duct and at a distance of at least twice the
width of the duct from bends and six times the
width from branches (see fig. 3).
The housing is opened without the use of tools
by pressing the snap lock beside the tube con-
nectors.
Cable connection
The output from the PTH is either voltage or
current controlled. The PTH must be provided
with a 24 VAC/DC power supply, see figure 4.
Setup menu
Use the buttons
, and OK to navigate
the menu. The buttons can be found on the
backside o the lid. The menu is divided into
three parts - Setup [ Set ], Relay [ ReL ] and
Calibration [ CAL ]. Follow the menu scheme in
figure 1 from the bottom up. Note the shown
menues depends en the selection of Pressure
or flow mode.
Setup - Pressure or flow mode [
]
Use Setup menu 1 to choose between Pressure
or Flow mode.
Setup - Pressure range [
]
Use Setup menu 2 to enter the pressure range.
Pressure range defines the pressure at which
the analogue output reaches the maximum
value.
Setup - Pressure setpoint [
]
Use Setup menu 3 to enter the pressure set-
point. Minimum is 0 Pa and maximum is 2500
Pa.
Setup - k-factor [
]
Use Setup menu 4 to enter the k-factor. The
scale is 0.001 to 9999. The dot position shall
be set before entering the value. The selected
dot position will also apply to the display, when
showing the current flow. After entering the
k-factor, place the correct unit stamp on the
PTH front.
Setup - Flow range [
]
Use Setup menu 5 to enter the flow range. Flow
range defines the flow at which the analogue
output reaches the maximum value.The dot
position shall be set before entering the value.
The selected dot position will also apply to the
display, when showing the current flow.
Setup - Flow setpoint [
]
Use Setup menu 6 to enter the air flow setpoint.
The scale is 0.000 to 9999.
Setup - Damping [
]
Use Setup menu 7 to enter the damping.
Minimum damping is 1 seconds and maximum
damping is 30 seconds. A low damping can
result in unsteady readings, while a higher
damping gives a more steady reading but also
a slower response time for the regulation. PTH
uses a ±2% dynamic average correction.
Setup - Analog output type [
]
Use Setup menu 8 to enter the analog output
mode. It is possible to switch between 0 - 10
VDC, 0 - 20 mA, 2 - 10 VDC and 4 - 20 mA as
transmitter output.
Relay menu
Relay - Activation delay [
]
Use Relay menu 1 to enter the relay activation
delay. Minimum delay is 0 seconds and maxi-
mum delay is 3600 seconds.
Relay - Hysteresis [
]
Use Relay menu 2 to enter the pressure
hysteresis. Minimum hysteresis is 1% and
maximum hysteresis is 50% of the pressure /
flow setpoint.
Relay - Invert relay [
]
Use Relay menu 3 to invert the default output
state for the relay. This feature allow applica-
tions where an alarm can be sent both on out of
range and on power supply failure. Invert relay
has to be set to ON to obtain this function.
Relay - Invert LED [
]
Use Relay menu 4 to invert the default LED
colour from Green to Red. This feature is useful
when the PTH is used as a pressure guard
when controlling a heater element. Here, the
LED should be Red until the setpoint is reached.
Calibration menu
When calibrating, make sure the PTH are in a
pressure free environment. To obtain a pressure
free enviroment remove the two air tubes on the
PTH. For caution reasons, each calibration will
only calibrate ±5 Pa.
Calibration [
]
Use Calibration menu 1 to calibrate. Confirm by
pressing [
].
Factory reset [
]
Use Calibration menu 2 to set the PTH back to
factory reset. Confirm by pressing [
].
LED INDICATOR
An LED on the front side of the PTH indicates
the operating status. Operating range is defined
as the setpoint ±hysteresis.
Non-inverted LED: A red light indicates that
the operating range has not been reached.
Conversely, a green light indicates that the
operating range has been reached.
Inverted LED: A green light indicates that the
current pressure/flow is below the operating
range. Conversely, a red light indicates that the
pressure/flow is above the operating range.
A flashing red light indicates that an error is ac-
tive. See Troubleshooting for more information.
TECHNICAL DATA
Supply voltage ............. 24 V~/=, ± 15%, 50/60 Hz
Relay .......................................... SPDT 30V~/=, 1A
Power consumption .......................................0.5 W
With relay active .............................................1.0 W
Output ..........0-10 V=, 2-10 V=, 0-20 mA, 4-20 mA
Accuracy relay setpoint* ........0.5% × MV* ± 2.5 Pa
Accuracy* .......1,5 % x MV* + 0,3% x SR* + 2,5 Pa
Measuring range, pressure .....................0-2500 Pa
Maximum pressure ....................................... 30 kPa
Maximum load
0 – 10 V= ...................................................... >2.5kΩ
0 – 20 mA ....................................................<=450Ω
Housing dimensions (h×w×d) ...... 91 × 75 × 38mm
Cable dimension ...................................... ø3-10mm
Connection
7 x spring terminals max 1.5mm²
Pressure tubes .....................................2 × ø6,2 mm
Environment Data
Storage temperature ....................... -40°C to +70°C
Operating
temperature............. -20°C to +40°C (continuous)**
-30°C to +70°C (short-term)***
Operating
humidity .......10%RH to 95%RH, non-condensing
Operating altitude .......................................≤2000m