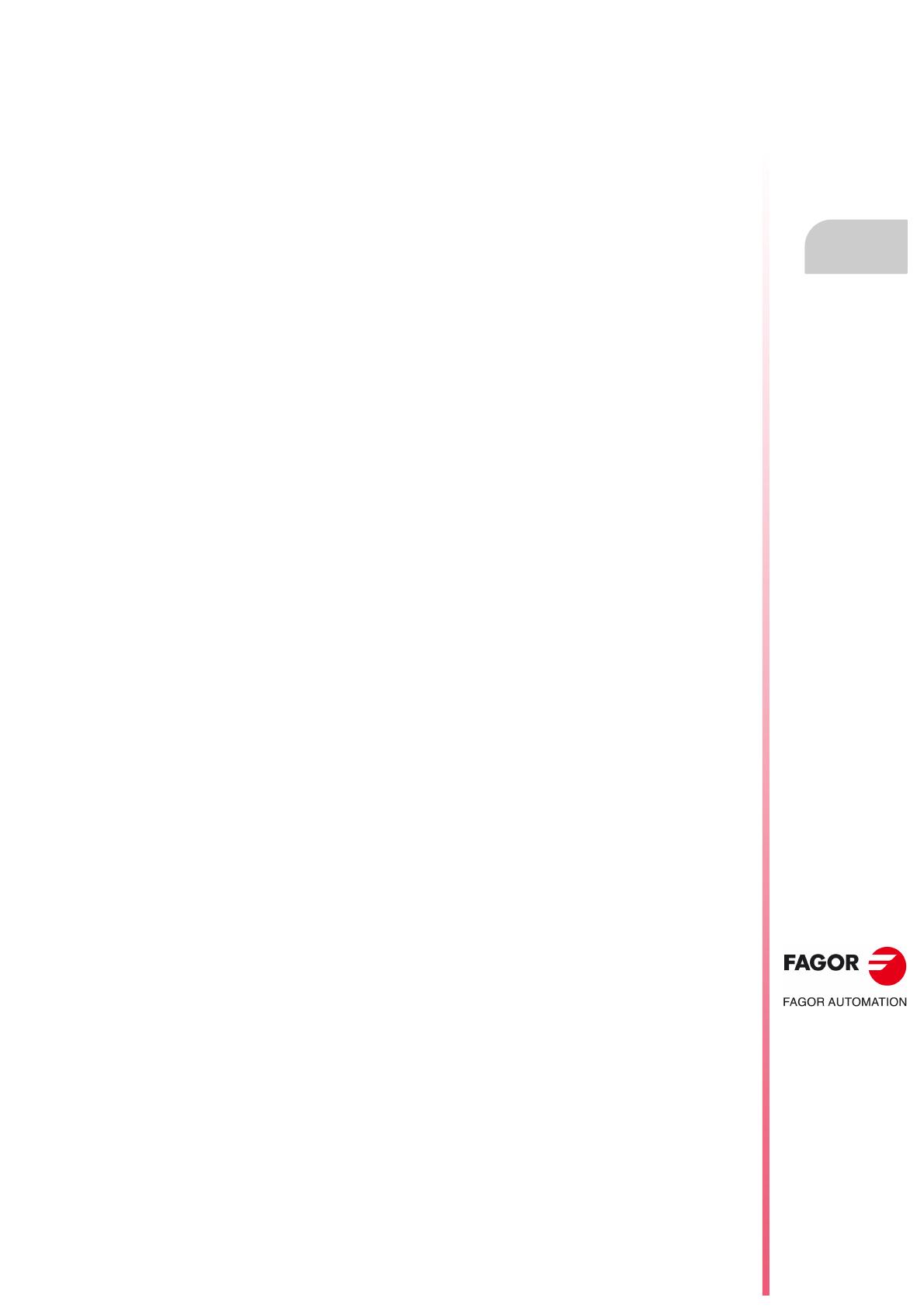
Módulos remotos.
CNC 8070
·7·
(REF: 1906)
SOFT C AXIS
Eje C.
Activa la cinemática para trabajar con eje C y sus ciclos
fijos asociados. El CNC puede controlar varios ejes C. Los
parámetros de cada eje indican si funcionará como un eje
C o no, y no será necesario activar otro eje en los
parámetros máquina.
SOFT TANDEM AXES
Ejes tándem.
Un eje tándem consiste en dos motores acoplados
mecánicamente entre sí formando un único sistema de
transmisión (eje o cabezal). Un eje tándem permite
disponer del par necesario para mover un eje cuando un
sólo motor no es capaz de suministrar el par suficiente
para hacerlo.
Al activar esta característica, debe tenerse en cuenta que
para cada eje tándem de la máquina, debe añadirse otro
eje a toda la configuración. Por ejemplo, en un torno
grande de 3 ejes (X Z y contrapunto), si el contrapunto es
un eje tándem, la orden de compra final de la máquina
debe indicar 4 ejes.
SOFT SYNCHRONISM
Sincronización de ejes y cabezales.
Los ejes y los husillos pueden sincronizarse de dos
maneras, en velocidad o en posición. La configuración
CNC contempla sincronizar 2 ejes o 2 cabezales. Una vez
sincronizados, sólo se visualiza y programa el elemento
el maestro.
SOFT HSSA II MACHINING SYSTEM
Sistema de mecanizado HSSA-II.
Es la nueva versión de algoritmos para el mecanizado de
alta velocidad (HSC). Este nuevo algoritmo HSSA permite
optimizar el mecanizado a alta velocidad, logrando
mayores velocidades de corte, contornos más suaves,
mejor acabado superficial y mayor precisión.
SOFT TANGENTIAL CONTROL
Control tangencial.
El control tangencial mantiene un eje giratorio siempre en
la misma orientación con respecto a la trayectoria
programada. La trayectoria de mecanizado está definida
en los ejes del plano activo y el CNC mantiene la
orientación del eje giratorio a lo largo de toda la
trayectoria.
SOFT DRILL CYCL OL
Ciclos ISO de taladrado para el modelo OL.
Ciclos ISO de taladrado para el modelo OL (G80, G81,
G82, G83).
SOFT PROBE
Ciclos fijos de palpador.
El CNC puede tener configurados dos palpadores;
habitualmente será un palpador de sobremesa para
calibrar herramientas y un palpador de medida para
realizar mediciones en la pieza.
Esta opción activa las funciones G100, G103 y G104 (para
realizar movimientos del palpador); los ciclos fijos de
palpador no están incluidos.
SOFT THIRD PARTY CANOPEN
CANopen de terceros.
Habilita el uso de módulos CANopen no-Fagor.
SOFT FVC UP TO 10m3
SOFT FVC MORE TO 10m3
Compensación volumétrica media y grande.
Las máquinas de 5 ejes se usan generalmente para
fabricar piezas grandes. La precisión de las piezas está
limitada por las tolerancias de fabricación de la máquina
y por el efecto de la temperatura durante el mecanizado.
En industrias como el aeroespacial, las demandas de
mecanizado hacen insuficientes las herramientas
clásicas de compensación. La compensación volumétrica
FVC viene para complementar las herramientas de ajuste
de la máquina. Al mapear el volumen de trabajo total de
la máquina, el CNC conoce la posición exacta de la
herramienta en todo momento. Después de aplicar las
compensaciones necesarias, la pieza resultante tiene la
precisión y tolerancia deseadas.
Hay 2 opciones dependiendo del tamaño de la máquina,
hasta 10 m³ y más de 10 m³.
SOFT 60 PWM CONTROL
Pulse-Width Modulation.
Esta función sólo está disponible en sistemas de
regulación con bus Sercos. Está orientada principalmente
a máquinas láser para el corte de chapa muy gruesa,
donde el CNC genera una serie de impulsos PWM para
controlar la potencia del láser al perforar el punto de
partida.
Esta característica es imprescindible para el corte de
chapa muy gruesa y requiere de dos salidas digitales
rápidas disponibles en la unidad central. Con esta nueva
característica, el OEM no necesita instalar dispositivos
externos y programarlos, reduciendo así el costo de la
máquina y el tiempo de instalación. El usuario final
también se beneficia porque la función "Cortar con PWM"
es mucho más fácil de usar y programar.
SOFT 60 GAP CONTROL
Control de gap.
Está orientada principalmente a máquinas láser. El control
del gap permite mantener una distancia fija entre la
boquilla del láser y la superficie de la chapa. Esta distancia
la calcula un sensor conectado al CNC, de manera que el
CNC compensará las variaciones del sensor sobre la
distancia programada con movimientos adicionales en el
eje programado para el gap.
SOFT DMC
Dynamic Machining Control.
El DMC adapta el avance durante el mecanizado para
mantener la potencia de corte lo más cercana posible a
las condiciones idóneas de mecanizado.
SOFT FMC
Fagor Machining Calculator.
La aplicación FMC consiste en una base de datos de
materiales a mecanizar y operaciones de mecanizado
(fresado y torneado), junto a un interface que permite
elegir las condiciones de corte adecuadas para dichas
operaciones.
SOFT FFC
Fagor Feed Control.
Durante la ejecución de un ciclo fijo del editor, la función
FFC permite sustituir el avance y velocidad programados
en el ciclo por los valores activos en la ejecución,
afectados por el feed override y speed override.
SOFT 60/65/70 OPERATING TERMS
Licencia de uso temporal.
La opción "Operating Terms" activa una licencia de uso
temporal en el CNC, válida hasta una fecha determinada
por el OEM.