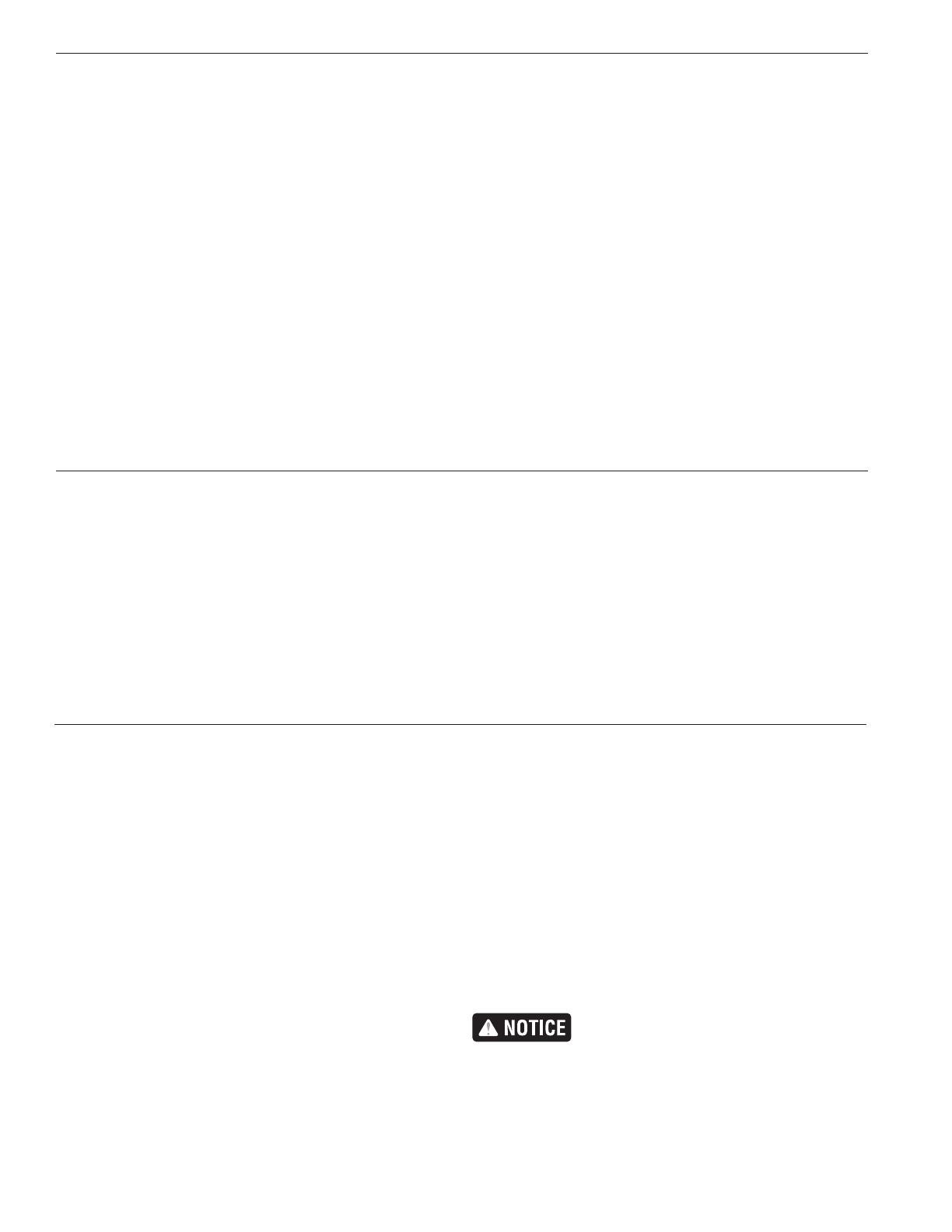
Introduction
Thank you for choosing Bernard. The product you have purchased has
been carefully assembled and factory tested prior to shipment. Should
you experience problems with installation or performance, please refer
to the “Troubleshooting Guide” in this manual.
Before installing, compare the equipment received against the invoice
to verify that the shipment is complete and undamaged. It is the
responsibility of the purchaser to file all claims of damage or loss that
may have occurred during transit with the carrier.
The manual contains general information on the operation of this
Bernard product. Before installing or operating any equipment, read
and understand the information and safety precautions presented
in this manual. Also, note the various data plates, labels, and tags
attached to the product.
While every precaution has been taken to assure the accuracy of this
manual, Bernard assumes no responsibility for errors or omissions.
Bernard assumes no liability for damages resulting from the use of
the information contained herein. Bernard shall have no liability to
the buyer for consequential damages or be liable to the in tort for
any negligent manufacture of the goods or for the omissions of any
warning therefrom.
Commercial Warranty
Product is warranted to be free from defects in material and
workmanship for 1 year after the sale by an authorized Buyer. Straight
handles, straight handle switches and straight rear strain reliefs are
covered by a lifetime warranty.
Bernard reserves the right to repair, replace or refund the purchase
price of non-conforming product. Product found not defective will be
returned to the Buyer after notification by Customer Service.
Bernard makes no other warranty of any kind, expressed or implied,
including, but not limited to the warranties of merchantability or fitness
for any purpose. Bernard shall not be liable under any circumstances
to Buyer, or to any person who shall purchase from Buyer, for
damages of any kind. Including, but not limited to any, direct, indirect
incidental or consequential damages or loss of production or loss of
profits resulting from any cause whatsoever, including, but not limited
to, any delay, act, error or omission of Bernard.
Genuine Bernard parts must be used for safety and performance
reasons or the warranty becomes invalid. Warranty shall not apply
if accident, abuse, or misuse damages a product, or if a product is
modified in any way except by authorized Bernard personnel.
Part I General Description
The Bernard PipeWorx MIG Gun is designed primarily for process-
ing mild steel electrode under GMAW (Gas Metal Arc Welding), MIG
(Metal Inert Gas), MAG (Metal Active Gas), FCAW (Flux Cored Arc
Welding), and MOG (Metal without Gas).
The PipeWorx MIG Gun provides rapid neck interchangeability, typi-
cally during production processes. Neck may also be positioned on
line within a 360 degree rotation. This position allows for movements
between standard horizontal welding, overhead, and hard-to-reach
side angles. The neck includes an optional jump liner system that
effectively reduces costs associated with one-piece liner systems.
Bernard is concerned about your higher productivity.
The PipeWorx MIG Gun meets or exceeds NEMA (National Electrical
Manufacturer’s Association) EW3 requirements for guns used in a
wide variety of applications including aluminum, silicone bronze, and
hard facing alloys to name a few. With Bernard’s flexibility, many ap-
plications can be accommodated with field installed options increasing
performance and maneuverability.
1. Your gun has been shipped with a specific feeder connector,
neck, and sized for electrode as per the part number indi-
cated on its package. Please inspect the received gun against
this part number for accuracy.
2. Turn off power prior to any installation.
3. Fully extend gun and cable. Press liner fully into power pin.
4. Safely expose approximately 2” (51 mm) of electrode
beyond feeder or adaptor block.
5. Power Pin
Connect the power pin of the direct plug gun by sliding
the electrode into the liner and the power fitting into the
drive housing of the feeder. Fully seat the unit in position
and tighten into place as designated in the manufacturer’s
instructions. On initial installations, a thin film of silicone
lubricant will aid installation and prevent o-ring damage.
Attach control lead wires to the appropriate plug, terminals,
or lead kit. Plug or wire into the control circuit of the feeder
as designated in manufacturer’s instructions.
If a gas hose is provided, connect to the feeder’s solenoid
circuit to deliver shielding gas to the arc. If no gas hose is
provided, gas is delivered through the power pin. Refer to
the manufacturer’s instructions for proper gas connection at
the feeder block or solenoid.
6. Remove nozzle from head assembly.
7. Pull contact tip from head/gas diffuser. An unobstructed
electrode path has now been established.
8. Safely feed electrode through the gun and approximately 1”
(25 mm) beyond head/gas diffuser.
9. Reinstall the contact tip over the electrode and lock into
position by reinstalling the nozzle.
Welding current and duty cycle
shall not exceed published
specication of this product. If such
conditions exist, product life and
performance will be reduced.
Part II Installation