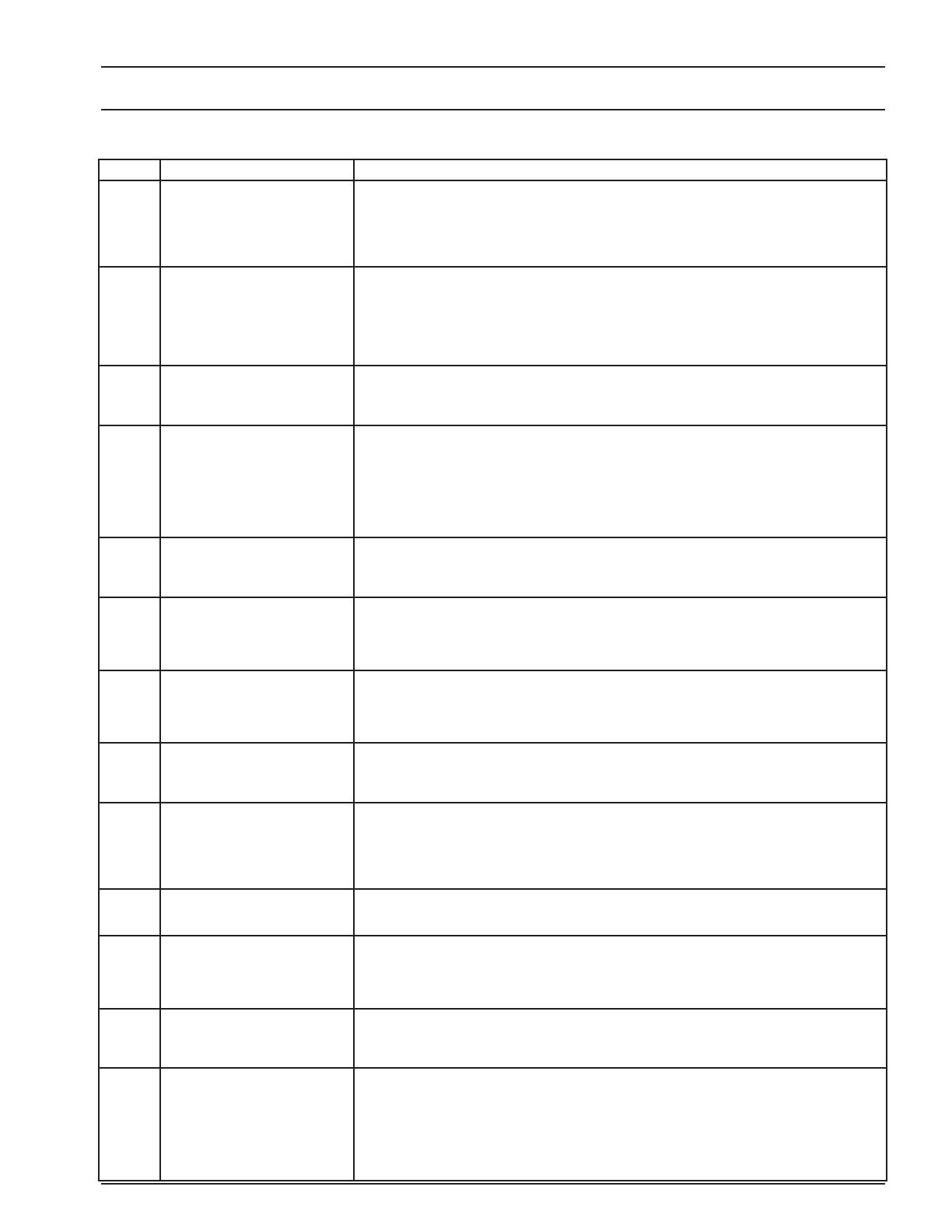
Maintenance/ troubleshooting
149
CAN PS Errors
Error code Problem Solution
01 Supply Line Voltage exceeded or
dropped below + / - 15% of rated input
when machine is in Idle mode
1. Check the input voltage to the machine with a voltage meter.
2. Check the input power cable for correct size and resistance.
3. Check the Main Transformer (T1) voltage tapping connections.
4. Check the input fuses in the PS.
5. Check the input line fuses in the disconnect box.
6. Check the multi-color ribbon cable between J12 on PCB1 and J2 and PCB2.
02 Supply Line Voltage exceeded or
dropped below + or - 20% of rated
input while cutting
1. Check the input line voltages to the machine with a voltage meter.
2. Check the input power cable for correct size and resistance.
3. Check the Main Transformer (T1) voltage tapping connections.
4. Check the input fuses in the PS.
5. Check the input line fuses in the disconnect box.
6. Check the multi-color ribbon cable between J12 on PCB1 and J2 and PCB2.
7. Notify your power company of the line stiness issues.
03 Control Transformer not supplying
proper voltage to control board or the
+24 and +/-15 volt bias supplies are not
balanced
1. Check the input voltage taps on the control transformer.
2. Check the control transformer output voltages on TB3, if the voltages read within +/-15% of the specied value
then replace the control board else replace control transformer.
04 There is a thermal fault inside the
Plasma Console. Fix any coolant ow
errors before investigating this error.
1. Wait 10 minutes for the unit to cool. If the thermal fault clears on its own then check for the ambient tempera-
ture being above 40C or dirt in the radiators.
2. Check if main fan is functioning and it is pulling air through the Plasma Console.
3. Shut o the Plasma Console and allow the machine to cool.
4. Check the diode bridge for an open thermal switch. If the switch is still open after certain time then replace
the switch.
5. Check the IGBT module for an open thermal switch. If the switch is still open after certain time then replace
the switch.
05 CYCLE START signal is high while the
power source is booting up.
1. Check the start signal to the Plasma Console while the Plasma Console is OFF. If there is voltage on the input,
nd and x the wiring error.
2. Check the start signal to the Plasma Console while the Plasma Console is ON. If there is voltage on the input
while CNC is OFF, check the Plasma Console control wiring for a short to the input.
06 Failed to re/ ignition did not take place
within 4 seconds after HF is turned ON.
1. Check the distance from the work piece matches the recommended ignition height.
2. Check the electrical connection from the work piece to the work connection on the Plasma Console.
3. Check the HF relay inside the Plasma Console.
4. Check the 115VAC voltage on the control transformer.
5. Check the consumables.
08 Torch error/Electrode current was pres-
ent before the PWM was enabled.
1. Check the jumper inside the RAS box between pins L and J on the 14-pin Amphenol connector.
2. Check for short between electrode and nozzle.
3. Check the IGBT gate pulse voltage connection on the driver board.
4. Check for shorted IGBT.
5. Check for shorted diode (D9).
09 Arc voltage is greater than 40V in Idle
mode.
1. Check for shorted IGBT.
2. Check for shorted diode (D9).
3. Check the arc voltage feedback connection on the driver board from the Electrode (-) terminal.
4. Check IGBT gate pulse voltage connection on the driver board.
11 Output current is greater than the
minimum idle current.
1. Check for shorted IGBT.
2. Check for shorted diode (D9).
3. Check the IGBT gate pulse voltage connection on the driver board. If there is positive voltage then replace the
driver board.
4. Check the hall sensors and their connections to the control board.
5. Replace the control board.
12 A phase of the input power is missing. 1. Check the fuses in the disconnect box for bad fuse.
2. Check the main contactor contacts for any damage.
3. Verify the input to the Plasma Console is providing all 3 phases.
13 Open circuit voltage did not reach 280
volts within 200 msec.
1. Check for short between the electrode and nozzle.
2. Check for short between the electrode cable and a connection to the work output of the Plasma Console.
3. Check for an open IGBT.
4. Check the IGBT gate pulse voltage connection on the driver board.
5. Check the multi-color ribbon connection from J12 on PCB1 to J2 on PCB2.
14 Ambient temperature exceeded 75° C
in control enclosure.
1. Check the temperature inside the control panel, if it reads below 55C and still the error is present then replace
the control board.
2. Cool the area around the Plasma Console to below 40C. This is the upper limit of the rated operating range for
the Plasma Console.
15 Bus voltage failed to reach 200 VDC
with in 500 ms.
1. Check for faulty input fuse.
2. Check for shorted bus lter capacitor.
3. Check the bus charger contactor (K2) contacts and coil for any damage.
4. Check the bus-charger contactor relay (RB1-1) for failure.
5. Check bus charger resistors connections.
6. Check the ribbon cable connection between J6 and Relay Module (RB1).
7. Check the multi-color ribbon cable connection between J12 on PCB1 to J2 on PCB2.
8. Check the 24VAC supply on the control transformer.