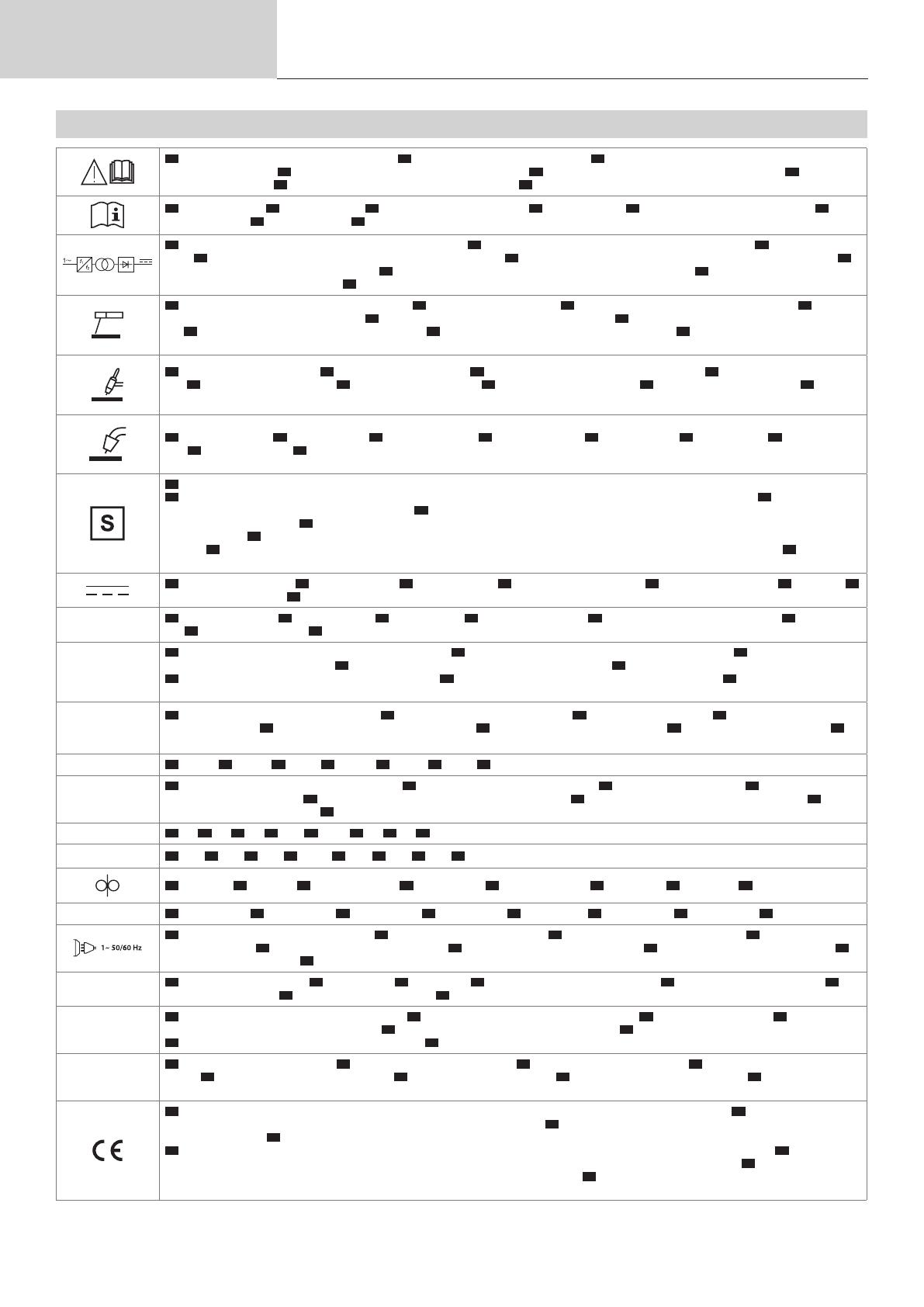
100
Pictogrammes KRONOS 250M
SYMBOLS / ZEICHENERKLÄRUNG / ICONOS / СИМВОЛЫ / PICTOGRAMMEN / ICONE
FR
Attention ! Lire le manuel d’instruction avant utilisation.
EN
Warning ! Read the user manual before use.
DE
ACHTUNG ! Lesen Sie diese Anleitung sorgfältig durch vor
Inbetriebnahme des Geräts.
ES
¡Atención! Lea el manual de instrucciones antes de su uso.
RU
Внимание! Прочтите инструкцию перед использованием.
NL
Let op! Lees
aandachtig de handleiding.
IT
Attenzione! Leggere il manuale d’istruzioni prima dell’uso.
PL
Uwaga! Przed użyciem należy uważnie przeczytać instrukcję obsługi.
FR
Symbole de la notice
EN
User manual symbol
DE
Symbole in der Bedienungsanleitung
ES
Símbolo del manual
RU
Символы, использующиеся в инструкции
NL
Symbool handleiding
IT
Simbolo del manuale
PL
Symbol ulotki
FR
Source de courant de technologie onduleur délivrant un courant continu.
EN
Undulating current technology based source delivering direct curent.
DE
Invertergleichstrom-
quelle.
ES
Fuente de corriente de tecnología ondulador que libera corriente continua.
RU
Источник тока с технологией преобразователя, выдающий постоянный ток.
NL
Stroombron met UPS technologie, levert gelijkstroom.
IT
Fonte di corrente con tecnologia inverter che rilascia una corrente continua.
PT
Fonte de energia da tecnologia do
inversor que fornece uma corrente contínua.
PL
Źródło prądu technologii falownika dostarczającego prąd stały.
FR
Soudage à l’électrode enrobée - MMA (Manual Metal Arc)
EN
MMA welding (Manual Metal Arc)
DE
Schweißen mit umhüllter Elektrode (E-Handschweißen)
ES
Soldadura
con electrodo revestido (MMA - Manual Metal Arc)
RU
Сварка электродом с обмазкой: MMA (Manual Metal Arc)
NL
Lassen met beklede elektrode - MMA (Manual Metal
Arc)
IT
Saldatura all’elettrodo rivestito - MMA (Manual Metal Arc)
PT
Soldadura a eletrodo revestido (MMA – Manual Metal Arc)
PL
Spawanie elektrodami otulonymi (MMA -
Manual Metal Arc)
FR
Soudage TIG (Tungsten Inert Gaz)
EN
TIG welding (Tungsten Inert Gas)
DE
TIG- (WIG-)Schweißen (Tungsten (Wolfram) Inert Gas)
ES
Soldadura TIG (Tungsten Inert
Gaz)
RU
Сварка TIG (Tungsten Inert Gaz)
NL
TIG lassen (Tungsten Inert Gaz)
IT
Saldatura TIG (Tungsten Inert Gaz)
PT
Soldadura TIG (Tungsten Inert Gaz)
PL
Spawanie
TIG ( Wolfram Gazu Obojętnego)
FR
Soudage à MIG / MAG
EN
MIG / MAG welding
DE
MIG / MAG-Schweißen
ES
Soldadura MIG / MAG
RU
Сварка MIG / MAG
NL
MIG/ MAG lassen
IT
Saldatura MIG /
MAG
PT
Soldagem MIG / MAG
PL
Spawanie MIG / MAG
FR
Convient au soudage dans un environnement avec risque accru de choc électrique. La source de courant elle-même ne doit toutefois pas être placée dans de tels locaux.
EN
Suitable for welding in an environment with an increased risk of electric shock. However this a machine should not placed in such an environment.
DE
Geeignet für
Schweißarbeiten im Bereich mit erhöhten elektrischen Risiken.
ES
Adaptado para soldadura en lugar con riesgo de choque eléctrico. Sin embargo, la fuente eléctrica no debe
estar presente en dichos lugares.
RU
Подходит для сварки в среде с повышенным риском удара током. В этом случае источник тока не должен находиться в том же
самом помещении.
NL
Geschikt voor het lassen in een ruimte met verhoogd risico op elektrische schokken. De voedingsbron zelf moet echter niet in dergelijke ruimte worden
geplaatst.
IT
Conviene alla saldatura in un ambiente a grande rischio di scosse elettriche. L’origine della corrente non deve essere localizzata in tale posto.
PL
Nadaje się do
spawania w środowisku o zwiększonym ryzyku porażenia prądem. Samo źródło prądu nie może jednak być umieszczone w tego typu pomieszczeniach.
FR
Courant de soudage continu
EN
Direct welding current
DE
Gleichschweißstrom
ES
Corriente de soldadura continua.
RU
Постоянный сварочный ток
NL
Gelijkstroom
IT
Corrente di saldatura continuo
PL
Stały prąd spawania.
U0
FR
Tension assignée à vide
EN
Open circuit voltage
DE
Leerlaufspannung
ES
Tensión asignada en vacío
RU
Номинальное напряжение холостого хода
NL
Nullastspan-
ning
IT
Tensione nominale a vuoto
PL
Znamionowe napięcie próżniowe
X(40°C)
FR
Facteur de marche selon la norme EN60974-1 (10 minutes – 40°C).
EN
Duty cycle according to standard EN 60974-1 (10 minutes – 40°C).
DE
Einschaltdauer: 10
min - 40°C, richtlinienkonform EN60974-1.
ES
Ciclo de trabajo según la norma EN60974-1 (10 minutos – 40°C).
RU
ПВ% согласно норме EN 60974-1 (10 минут – 40°C).
NL
Inschakelduur volgens de norm EN60974-1 (10 minuten – 40°C).
IT
Ciclo di lavoro conforme alla norma EN60974-1 (10 minuti – 40°C).
PL
Cykl pracy zgodny z normą
EN60974-1 (10 minut - 40 ° C)
I2
FR
Courant de soudage conventionnel correspondant
EN
Corresponding conventional welding current
DE
Entsprechender Schweißstrom
ES
Corriente de soldadura conven-
cional correspondiente.
RU
Соответствующий номинальный сварочный ток
NL
Corresponderende conventionele lasstroom
IT
Corrente di saldatura convenzionale.
PL
Odpowiedni konwencjonalny prąd spawania
A
FR
Ampères
EN
Amperes
DE
Ampere
ES
Amperios
RU
Амперы
NL
Ampère
IT
Amper
U2
FR
Tensions conventionnelles en charges correspondantes
EN
Conventional voltage in corresponding loads.
DE
Entsprechende Arbeitsspannung
ES
Tensiones convencio-
nales en cargas correspondientes.
RU
Номинальные напряжения при соответствующих нагрузках.
NL
Conventionele spanning in corresponderende belasting
IT
Tensioni
convenzionali in cariche corrispondenti
PL
Ampery
V
FR
Volt
EN
Volt
DE
Volt
ES
Voltio
RU
Вольт
NL
Volt
IT
Volt
PL
Wolt
Hz
FR
Hertz
EN
Hertz
DE
Hertz
ES
Hercios
RU
Герц
NL
Hertz
IT
Hertz
PL
Herc
FR
Vitesse du l
EN
Wire speed
DE
Drahtgeschwindigkeit
ES
Velocidad de hilo
RU
Скорость проволоки
NL
Draadsnelheid
IT
Velocità di lo
PL
Prędkość drutu
m/min
FR
Mètre par minute
EN
Meter per minute
DE
Meter pro Minute
ES
Metro por minuto
RU
Метр в минуту
NL
Meter per minuut
IT
Metro per minuto
PL
Metr na minutę
FR
Alimentation électrique monophasée 50 ou 60Hz
EN
Single phase power supply 50 or 60 Hz
DE
Einphasige Netzversorgung mit 50 oder 60Hz
ES
Alimentación eléctrica
monofásica 50 o 60Hz
RU
Однофазное электропитание 50 или 60Гц
NL
Enkelfase elektrische voeding 50Hz of 60Hz.
IT
Alimentazione elettrica monofase 50 o 60Hz
PT
Alimentação monofásica 50/60Hz
PL
Zasilanie jednofazowe 50 lub 60Hz.
U1
FR
Tension assignée d’alimentation
EN
Assigned voltage
DE
Netzspannung
ES
Tensión asignada de alimentación eléctrica.
RU
Номинальное напряжение питания
NL
Nominale voedingsspanning
IT
Tensione nominale d’alimentazione
PL
Napięcie znamionowe zasilania.
I1max
FR
Courant d’alimentation assigné maximal (valeur efcace)
EN
Maximum rated power supply current (effective value).
DE
Maximaler Versorgungsstrom
ES
Corriente de
alimentación eléctrica asignada máxima (valor ecaz).
RU
Максимальный сетевой ток (эффективное значение)
NL
Maximale nominale voedingsstroom (effectieve waarde)
IT
Corrente d’alimentazione nominale massima (valore effettivo)
PL
Maksymalny prąd znamionowy zasilania (wartość skuteczna).
I1eff
FR
Courant d’alimentation effectif maximal
EN
Maximum effective power supply current.
DE
Maximaler effektiver Versorgungsstrom
ES
Corriente de alimentación eléctrica
máxima.
RU
Максимальный эффективный сетевой ток
NL
Maximale effectieve voedingsstroom
IT
Corrente effettivo massimo di alimentazione
PL
Maksymalny skuteczny
prąd zasilania
FR
Matériel conforme aux Directives européennes. La déclaration UE de conformité est disponible sur notre site (voir à la page de couverture).
EN
Device complies with euro-
peans directives, The EU declaration of conformity is available on our website (see cover page).
DE
Gerät entspricht europäischen Richtlinien. Die Konformitätserklärung nden
Sie auf unsere Webseite.
ES
Aparato conforme a las directivas europeas. La declaración de conformidad UE está disponible en nuestra página web (dirección en la portada).
RU
Устройство соответствует директивам Евросоюза. Декларация о соответствии доступна для просмотра на нашем сайте (ссылка на обложке).
NL
Apparaat in ove-
reenstemming met de Europese richtlijnen. De verklaring van overeenstemming is te downloaden op onze website (adres vermeld op de omslag).
IT
Materiale in conformità
alle Direttive europee. La dichiarazione di conformità è disponibile sul nostro sito (vedere sulla copertina).
PL
Urzadzenie jest zgodne z dyrektywami europejskimi. Deklaracja
Zgodności UE jest dostępna na naszej stronie internetowej (patrz strona tytułowa).