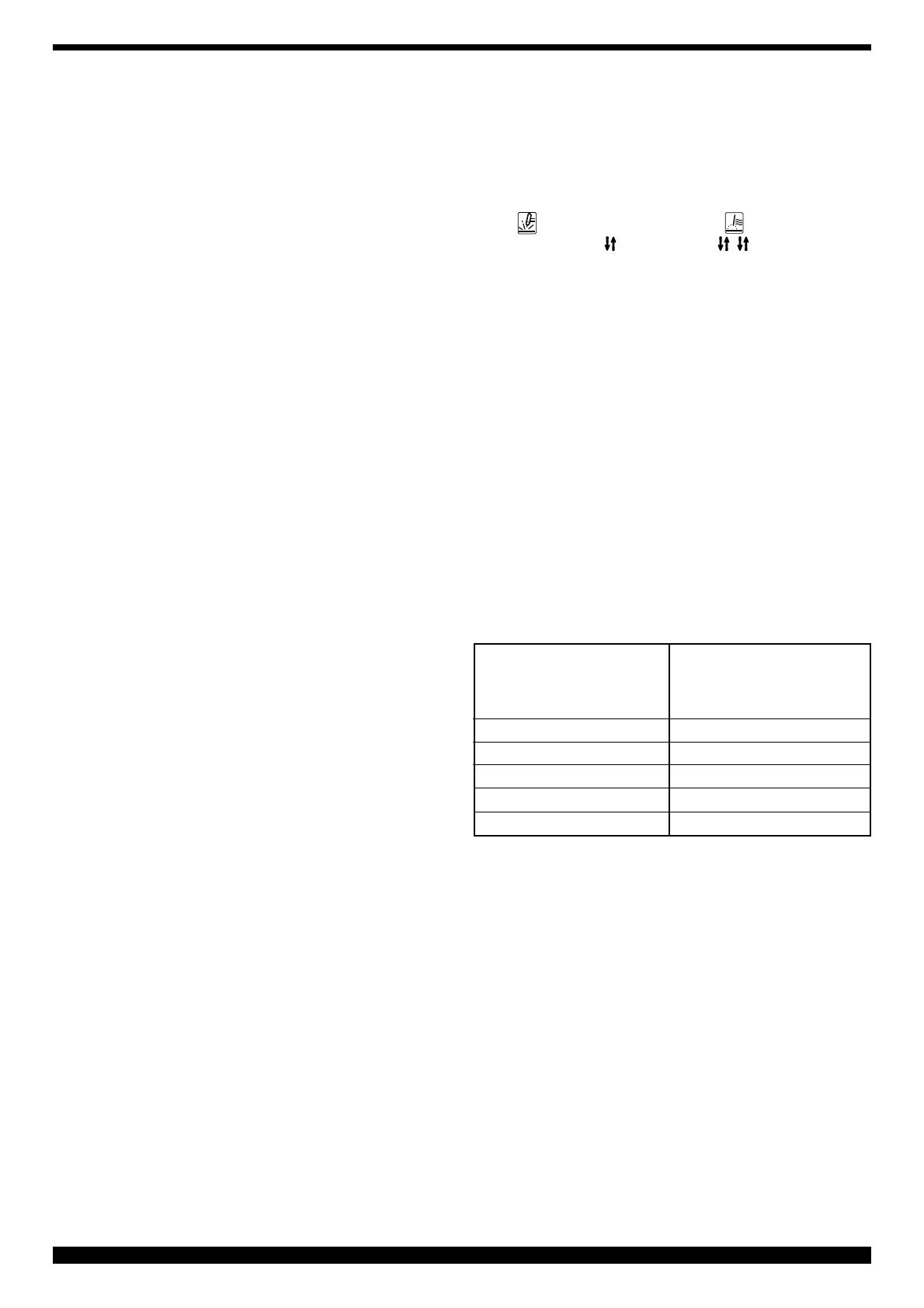
27
arranque de alimentación, por lo tanto, hay que adaptar los
cables para soldar respetando la polaridad exigida por el
fabricante de los electrodos que se usarán.
Conectar la pinza del cable de masa a la pieza de soldar.
• El circuito para soldar no se debe poner, deliberadamente
a contacto directo o indirecto con el conductor de protec-
ción, sino que solamente en el pedazo que hay que soldar
• Si el pedazo sobre el cual se trabaja, se coloca delibera-
damente a tierra, mediante el conductor de protección, la
conexión se deber hacer lo más directa posible y
realizada con un conductor de sección que sea igual al
del conductor de regreso de la corriente para soldar y
conectado al pedazo sobre el cual se trabaja, en el mismo
punto del conductor de regreso, utilizando el borne del
conductor de retorno o utilizando otro borne de masa que se
colocará lo más cerca posible.
• Hay que tomar todos las precauciones con el fin de
evitar corrientes de soldar dispersas.
• Controlar que la tensión de alimentación corresponda a la
tensión indicada en el letrero de los datos técnicos.
• Conectar el cable de alimentación a un enchufe de calibre
adecuado, asegurándose de que el conductor amarillo/
verde de alimentación esté conectado a la clavija de tierra.
• La capacidad del interruptor magnetotérmico o de los
fusibles en serie a la alimentación tiene que ser igual o
superior de la corriente I1 absorbida por la máquina.
• La corriente I1 absorbida se deduce de la lectura de los
datos técnicos colocados sobre la máquina y correspon-
diente a la tensión de alimentación U1 a disposición.
• Eventuales extensiones tienen que ser de las secciones
adecuadas a la corriente I, absorbida.
• Encender la maquina.
• No tocar partes bajo tensión
• No tocar los bornes de salida para soldar cuando la
máquina está encendida.
• No tocar contemporaneamente la torcha o el portaelectro-
do y el borne de la pieza.
• Regular la corriente de acuerdo al diametro del electrodo,
a la posición de soldadura y al tipo de junta que hay que
realizar.
Cuando se ha terminado la soldadura, hay que recordarse
siempre de apagar la máquina y de quitar el electrodo
de la junta portaelectrodo.
3.5 SOLDADURA TIG
• Con esta soldadora se puede soldar, usando el procedi-
miento TIG: el acero inoxidable, el hierro. el cobre.
• Conectar el conector del cable de masa al polo positivo (+)
de la soldadora y el borne al pedazo que se encuentre más
cerca de la soldadura, cerciorandose que exista un buen
contacto eléctrico.
• El circuito para soldar no se debe poner, deliberadamente
a contacto directo o indirecto con el conductor de protec-
ción, sino que solamente en el pedazo que hay que soldar.
• Si el pedazo en el cual se trabaja se coloca deliberadamen-
te a tierra mediante el conductor de protección, dicha
conexión se tiene que hacer lo más directa posible y
realizarla con un conductor de sección, al menos, igual al
del conductor de retorno de la corriente para soldar y
conectado al pedazo en el cual se trabaja en el mismo punto
del conductor de retorno, utilizando el borne del conductor
de retorno o utilizando otro borne de masa colocádolo lo
más cerca posible.
• Cada precaución tiene que ser tomada al fin de evitar
corrientes dispersas de soldadura.
• Utilizar la antorcha apta para la corriente de soldadura y
colocar el conector de potencia al polo negativo (-) de la
soldadora.
• Conectar el conector de la antorcha al conector F de la
soldadora.
• Conectar el empalme del tubo del gas del brazo con el
empalme I de la máquina y el tubo del gas que procede del
reductor de presión de la bombona con el empalme que se
halla en el panel posterior.
- Seleccionar mediante el pomo A el encendido por contacto
(roce)
o mediante alta frecuencia y la soldadura TIG
y el modo manual o automatico .
•
El flujo del gas inerte hay que regularlo con valor (litros
al minuto) a más o menos 6 veces el díametro del electrodo.
• Si se usan accesorios tipo gas-lens el paso de gas se
puede reducir a más o menos 3 veces el díametro del
electrodo.
• El díametro de la boquilla cerámica tiene que tener un
díametro de 4 o 6 veces el díametro del electrodo.
• Generalmente el gas que más se usa es el ARGON porque
tiene un costo menor respecto a los otros gas inertes,
pero también se pueden usar mezclas de ARGON con un
máximo de 2% de HIDROGENO para soldar el acero
inoxidable y el helio o mezcla de ARGON HELIO para
soldar el cobre. Estas mezclas aumentan el calor del arco
durante la soldadura pero son mucho más caras.
• Si se usa gas helio hay que aumentar los litros al minuto
de manera de obtener una proporción de 10 respecto al
díametro del electrodo (ejemplo:Ø1.6x10 = 16 lt./min.helio).
• Usar los vidrios de protección D.I.N. 10 hasta 75A y
D.I.N. 11 de 75A en adelante.
• Utilizar un electrodo de tungsteno toriado 2%, elegido de
acuerdo al cuadro siguiente y preparado como indicados in
3.6.1.
Ø ELECTRODO CORRIENTE CONTINUA
TUNGSTENO 2% TORIO ELECTRODO NEGATIVO
(BANDA ROJA) (ARGON)
ø 0.5 mm (0,020") 15¸40 A
ø 1 mm (0.040") 25¸85 A
ø 1,6 mm (0.060") 70¸150 A
ø 2.4 mm (0.095") 150¸250 A
ø 3.2 mm (0.130") 200¸350 A
• Controlar que la tensión de alimentación corresponda a la
tensión indicada en el letrero de los datos técnicos .
• Conectar el cable de alimentación a un enchufe de calibre
adecuado, asegurándose de que el conductor amarillo/
verde de alimentación esté conectado a la clavija de tierra.
• La capacidad del interruptor magnetotérmico o de los
fusibles en serie a la alimentación tiene que ser igual o
superior a la corriente I1 absorbida por la máquina.
• Eventuales extensiones tienen que ser de secciones
adecuadas a la corriente I1 absorbida.
• Encender la máquina.
• No tocar partes bajo tensión.
• No tocar los bornes de salida para soldar cuando la
máquina está encendida.
• No tocar al mismo tiempo la torcha y el borne de masa.
• Al final de la soldadura hay que recordarse de apagar
la máquina y de cerrar la válvula de la bombona del gas.
3.6.1 Preparación del electrodo
Hay que poner especial atención en la preparación de
la punta del electrodo, pulirla de manera que presente