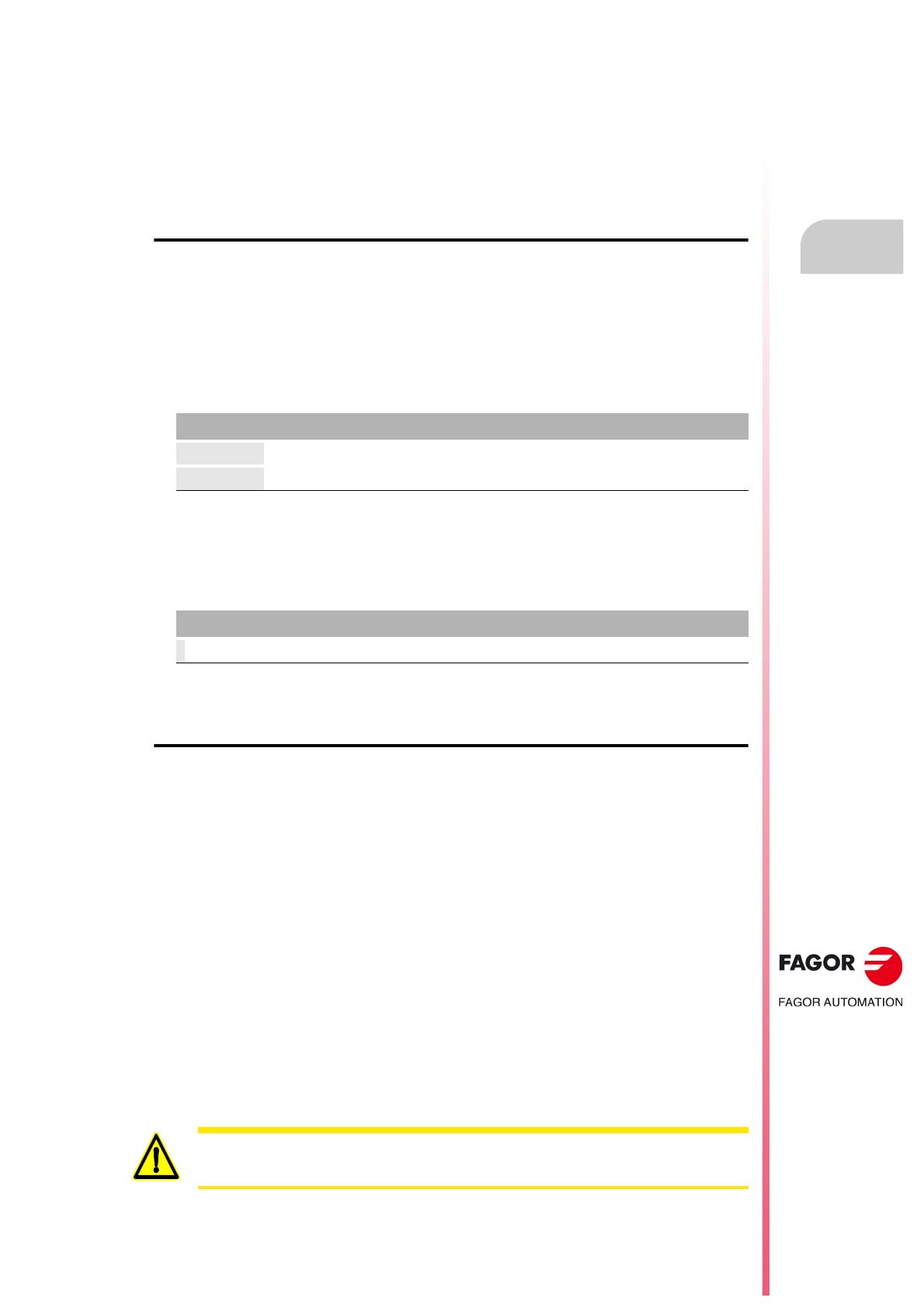
Nuevas prestaciones
CNC 8037
MODELO ·T·
S
OFT: V02.3X
·7·
3 Anticipación de funciones M
La prestación de anticipación de funciones M permite transferir al PLC una función M, antes de
terminar el movimiento anterior. Esta prestación es muy útil en máquinas punzonadoras. En estas
máquinas, permite preparar el siguiente punzonado desde el PLC antes de terminar el movimiento
anterior.
Definición de las funciones M a ejecutar anticipadamente
La tabla de funciones auxiliares M dispone de un campo formado por 8 bits de personalización.
Para definir cuales son las funciones M que se ejecutarán anticipadamente, utilizar el bit 5 de
personalización de las funciones M deseadas. El tiempo en el que se anticipan estas funciones M,
se indica en el parámetro máquina general MANTIME (P196).
Bit 5 de personalización de la tabla de funciones auxiliares M
Indica si la función auxiliar M se ejecuta anticipadamente.
MANTIME (P196)
Parámetro máquina general que indica el tiempo, en milisegundos, en el que se anticipan las
funciones auxiliares M indicadas mediante el bit 5 de personalización de la tabla de funciones
auxiliares M.
Consideraciones y limitaciones
Se pueden anticipar funciones M en G5, G7 y G50, pero no se pueden anticipar en G51.
Únicamente se anticipan funciones auxiliares M que se ejecutan desde el canal principal. Las
funciones M que se ejecutan desde el canal del PLC no se anticipan.
Sólo se anticipan las funciones auxiliares M que no tienen un significado predefinido para el CNC.
Las siguientes funciones M no se anticipan:
M0, M1, M2, M3, M4, M5, M6, M8, M9, M19, M30, M41, M42, M43, M44 y M45.
Sólo se anticipa una función auxiliar M si entre el bloque de movimiento previo y el bloque de la
función M no hay otros bloques de bajo nivel (F, G,...).
Las funciones M que se anticipan deben programarse solas en el bloque, no pueden programarse
junto con más funciones M, S ni T. En caso contrario, el CNC mostrará el error "La función M se
debe programar sola en el bloque".
Las funciones M que se anticipan podrán programarse en bloques de movimiento. Si la función M
está personalizada para ser ejecutada después del bloque de movimiento, podrá programarse el
conjunto (movimiento - M de punzonado) en el mismo bloque.
La anticipación de las funciones M sólo se realizará en modo ejecución. No se anticiparán funciones
M en ninguno de los modos de simulación.
Valor Significado
0 La función auxiliar M no se ejecuta anticipadamente.
1 La función auxiliar M sí se ejecuta anticipadamente.
Valores posibles
Números enteros entre 0 y 65535 ms.
Valor por defecto: 0 (no se ejecuta anticipadamente)
Si hay filtros parametrizados en los ejes, el tiempo de anticipación es mayor que el indicado en el
parámetro máquina general MANTIME (P196). En este caso, para conseguir un correcto
funcionamiento de la prestación, será necesario ajustar este parámetro.