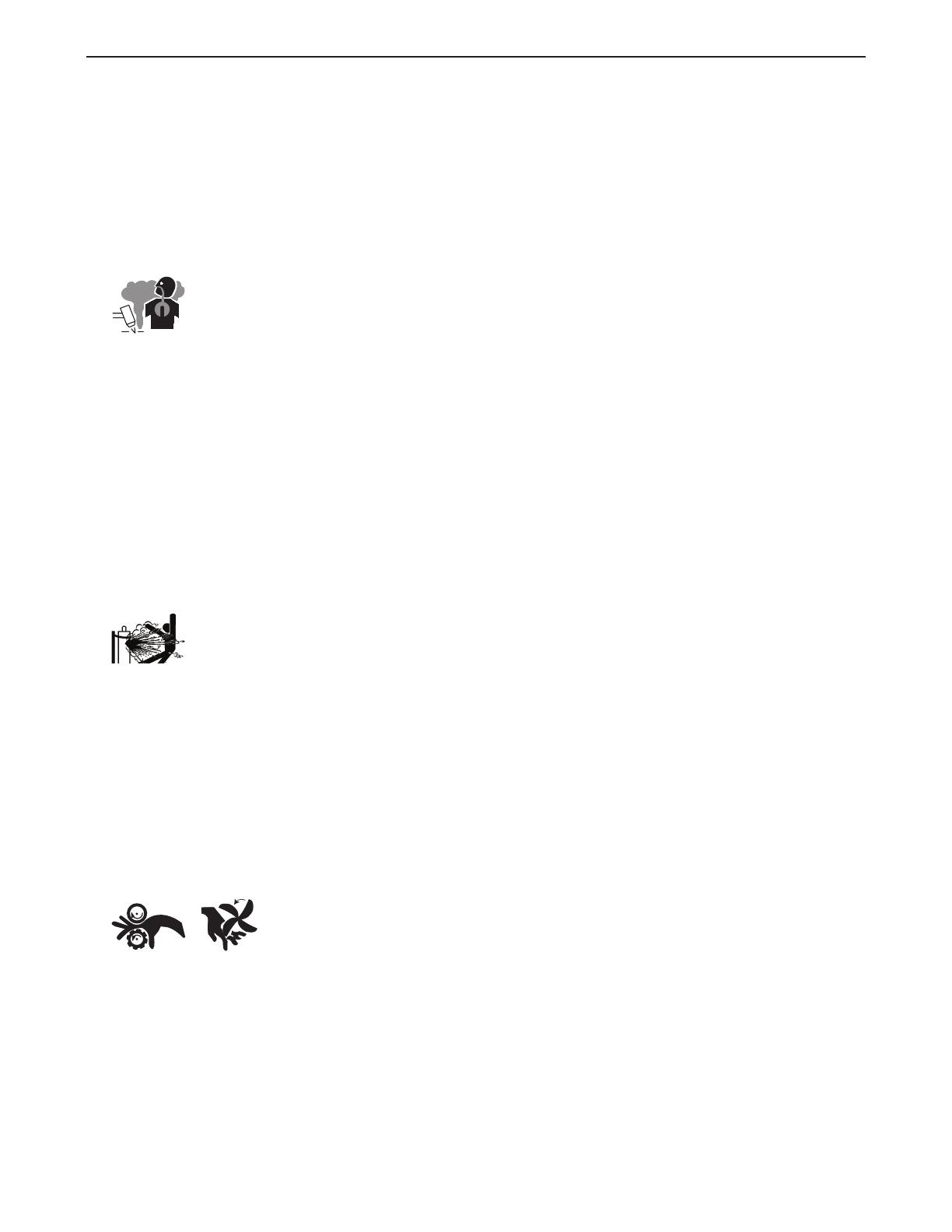
1 SEGURIDAD
0463 703 001ES
-9-
1. Los soldadores que tengan implantado un marcapasos deben consultar a su médico antes de soldar. Los campos
electromagnéticos (CEM) pueden interferir con algunos marcapasos.
2. La exposición a los CEM puede tener otros efectos en la salud que son desconocidos.
3. Los soldadores deben usar los siguientes procedimientos para minimizar la exposición a los CEM:
a) Tienda los cables de trabajo y del electrodo juntos. Fíjelos con cinta adhesiva cuando sea posible.
b) No se enrolle nunca el soplete o los cables de trabajo alrededor del cuerpo.
c) No coloque su cuerpo entre el soplete y los cables de masa. Tienda los cables solo a un lado de su cuerpo.
d) Conecte el cable de masa a la pieza lo más cerca posible de la zona de soldadura.
e) Mantenga la fuente de alimentación y los cables de soldadura tan alejados del cuerpo como sea posible.
HUMOS Y GASES
Los humos y los gases pueden provocar malestar o daños, especialmente en espacios reducidos.
Los gases de protección pueden provocar asxia. Por lo tanto:
1. Aleje su cabeza de los humos. No inhale los humos ni los gases.
2. La zona de trabajo debe disponer de una ventilación adecuada, generada de forma natural o con medios mecáni-
cos. No suelde, corte ni desbaste sobre materiales como el acero galvanizado, acero inoxidable, cobre, zinc, plomo,
berilio o cadmio a menos que haya ventilación mecánica positiva. No inhale los humos de estos materiales.
3. No trabaje cerca de operaciones de desengrase o aspersión. El calor o el arco pueden reaccionar con los vapores
de hidrocarburos clorados para formar fosgeno, un gas altamente tóxico y otros gases irritantes.
4. Si la ventilación no es la adecuada, puede causar irritaciones oculares, nasales y de garganta momentáneas. Detenga
el trabajo y realice los pasos necesarios para mejorar la ventilación de la zona de trabajo. No siga trabajando si el
malestar físico no desaparece.
5. Consulte la norma Z49.1 de ANSI/ASC acerca de las recomendaciones especícas de ventilación.
6. ADVERTENCIA: Este producto, cuando se usa para soldar o cortar, produce humos o gases que contienen sustancias
químicas que el Estado de California sabe que causan defectos de nacimiento y, en algunos casos, cáncer (Código
de Seguridad y Salud de la Ley del Estado de California §25249.5 y siguientes).
MANIPULACIÓN DE CILINDROS
Los cilindros, si no se manipulan bien, pueden romperse y soltar gas de forma violenta. La ruptura
repentina de la válvula del cilindro o del dispositivo de liberación puede producir lesiones o la
muerte. Por lo tanto:
1. Coloque los cilindros alejados de fuentes de calor, chispas y llamas. No golpee nunca un cilindro con un arco.
2. Utilice el gas adecuado para el proceso y la presión adecuada reduciendo el regulador diseñado para funcionar con
el cilindro de gas comprimido. No utilice adaptadores. Mantenga las mangueras y los acoplamientos en buenas
condiciones. Siga las instrucciones de funcionamiento del fabricante para montar el regulador en un cilindro de
gas comprimido.
3. Acople siempre los cilindros en posición vertical con una cadena o correa a las carretillas de mano, trenes de rodaje,
bancos, paredes, postes o portabultos correspondientes. No je nunca los cilindros a mesas de trabajo o soportes
que puedan formar parte de un circuito eléctrico.
4. Cuando no se utilicen, mantenga cerradas las válvulas del cilindro. Coloque la tapa de protección de la válvula si el
regulador no está conectado. Fije y mueva los cilindros usando las carretillas adecuadas.
PIEZAS EN MOVIMIENTO
Las piezas en movimiento, como los ventiladores, los rotores y las correas pueden causar
lesiones. Por lo tanto:
1. Mantenga los dispositivos de seguridad y las cubiertas de los armarios en su lugar y en buen estado.
2. Detenga el motor antes de instalar o conectar la unidad.
3. Solo las personas cualicadas pueden extraer las tapas cuando sea necesario para su mantenimiento y para solu-
cionar problemas
4. Para evitar el arranque accidental del equipo durante las operaciones de mantenimiento o servicio, desconecte el
cable negativo (-) de la batería.
5. Mantenga las manos, el pelo, la ropa holgada y las herramientas alejados de las partes móviles.
6. Vuelva a colocar los paneles o tapas y cierre las puertas cuando el servicio haya nalizado y antes de arrancar el
motor.