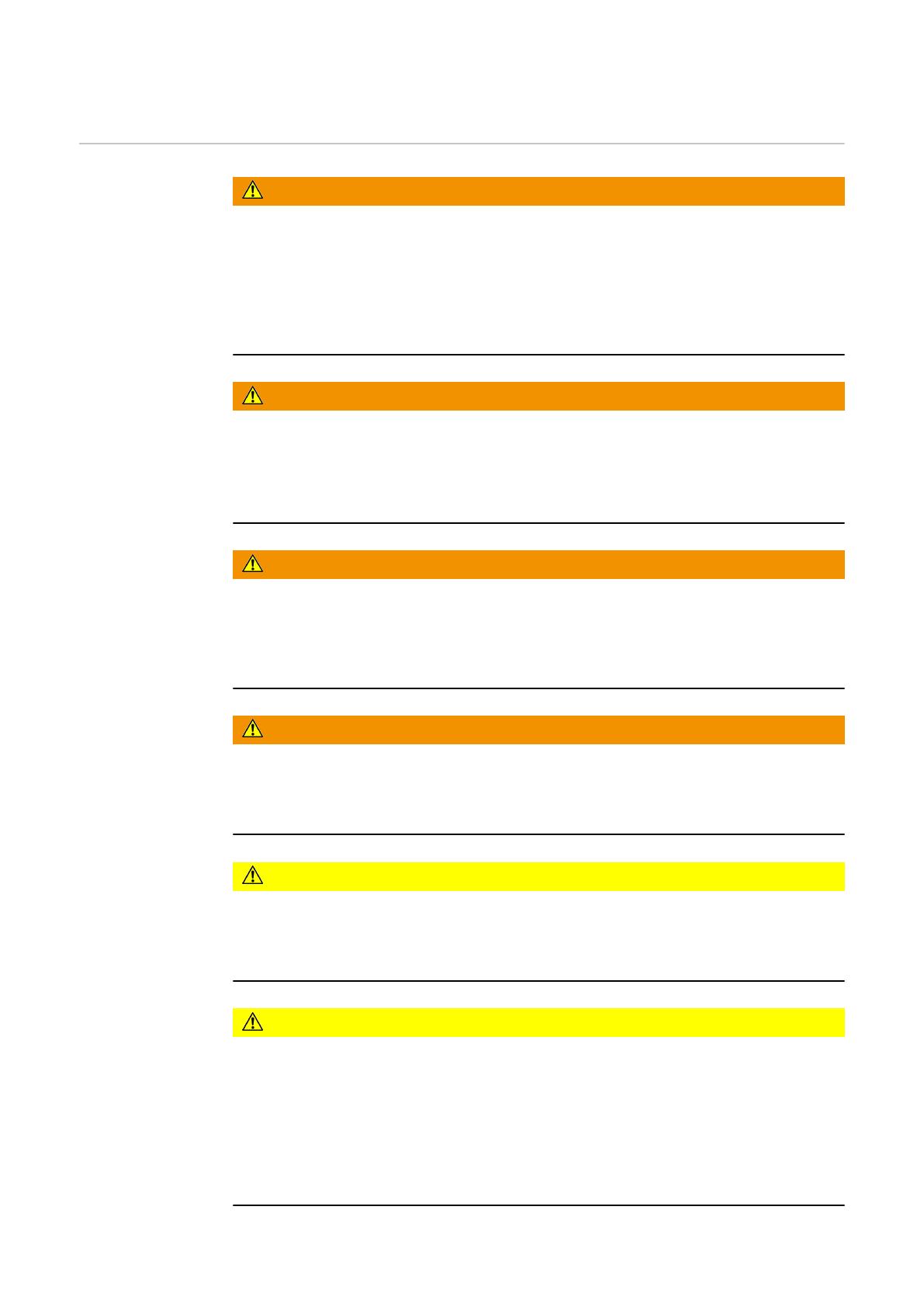
Safety
Safety WARNING!
Danger from incorrect operation and work that is not carried out properly.
This can result in severe personal injury and damage to property.
▶All the work and functions described in this document must only be carried out by
trained and qualified personnel.
▶Read and understand this document.
▶Read and understand all the Operating Instructions for the system components,
especially the safety rules.
WARNING!
Danger from electrical current and from emerging wire electrode.
This can result in severe personal injury and damage to property.
▶Before starting work, switch off all the system components involved and disconnect
them from the grid.
▶Secure all system components involved so they cannot be switched back on.
WARNING!
Danger from electric current due to defective system components and incorrect
operation.
This can result in severe personal injury and damage to property.
▶All cables, leads, and hosepacks must always be securely connected, undamaged,
correctly insulated, and adequately sized.
WARNING!
Danger from coolant leakage due to unsealed coolant hoses.
There may be a risk of slipping and damage to property.
▶When disconnecting a welding torch from the cooling unit or wirefeeder, always seal
the coolant hoses using the plastic seal attached to the torch.
CAUTION!
Danger due to hot welding torch components and coolant.
Serious burns may result.
▶Allow all welding torch components and the coolant to cool down to room temperatu-
re (+25 °C or +77 °F) before starting any of the work described in this document.
CAUTION!
Danger due to the operation of water-cooled welding torches without coolant.
This can result in damage to property.
▶Never use water-cooled welding torches without coolant.
▶During welding, ensure that the coolant is circulating correctly - this will be the case
if a regular return flow of coolant can be seen in the coolant container of the cooling
unit.
▶The manufacturer will not be liable for any damages due to non-observance of the
above mentioned points. All claims against the warranty are void.
36