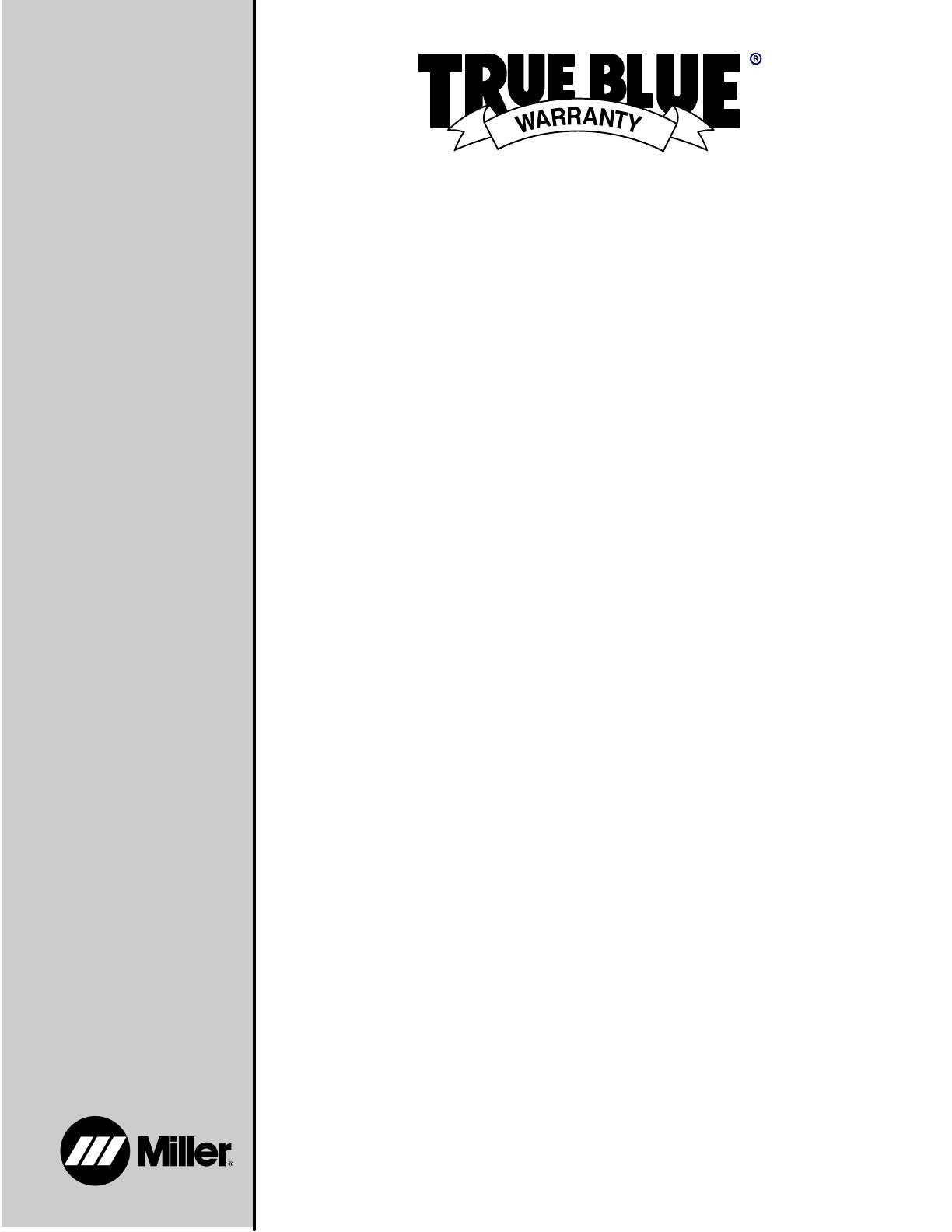
Efectivo 1 enero, 2017
(Equipo equipo con el número de serie que comienza con las letras “MH” o más nuevo)
Esta garantía limitada reemplaza a todas las garantías previas de Miller y no es exclusiva con otras garantías ya sea expresadas o supuestas.
GARANTÍA LIMITADA − Sujeta a los términos y condiciones de abajo,
la compañía MILLER Mfg. Co., Appleton, Wisconsin, garantiza al
primer comprador al por menor que el equipo de MILLER nuevo
vendido, después de la fecha efectiva de esta garantía está libre de
defectos en material y mano de obra al momento que fue embarcado
desde MILLER. ESTA GARANTÍA EXPRESAMENTE TOMA EL
LUGAR DE CUALQUIERA OTRA GARANTÍA EXPRESADA O
IMPLICADA, INCLUYENDO GARANTÍAS DE MERCANTABILIDAD,
Y CONVENIENCIA.
Dentro de los periodos de garantía que aparecen abajo, MILLER
reparará o reemplazará cualquier pieza o componente garantizado
que fallen debido a tales defectos en material o mano de obra.
MILLER debe de ser notificado por escrito dentro de 30 días de que
este defecto o fallo aparezca, en ese momento MILLER dará
instrucciones sobre el procedimiento para hacer el reclamo de
garantía que se debe seguir. Si la notificación se envía como una
reclamación por garantía en línea, dicha reclamación debe incluir una
descripción detallada de la fallo y los pasos seguidos para identificar
los componentes defectuosos y la causa de su fallo.
MILLER aceptará los reclamos de garantía en equipo garantizado que
aparece abajo en el evento que tal fallo esté dentro del periodo de
garantía. El período de garantía comienza la fecha que el equipo ha
sido entregado al comprador al por menor, o no exceder doce meses
después de mandar el equipo a un distribuidor en América del Norte o
dieciocho meses después de mandar el equipo a un distribuidor
internacional.
1. 5 años para piezas — 3 años para mano de obra
* Los rectificadores de potencia principales originales solo
incluyen los SCR, diodos y los módulos rectificadores
discretos
2. 3 años — Piezas y mano de obra
* Lentes para caretas fotosensibles (excepto serie Classic) (no
cubre mano de obra)
* Grupos soldadora/generador impulsado por motor de
combustión interna
(NOTA: los motores son garantizados separadamente por
el fabricante del motor.)
* Máquinas de soldar con inversor (excepto que se indique lo
contrario)
* Máquinas para corte por plasma
* Controladores de proceso
* Alimentadores de alambre automáticos y semiautomáticos
* Máquinas de soldar con transformador/rectificador
3. 2 años — Piezas y mano de obra
* Lentes para caretas fotosensibles − Solo serie Classic (no
cubre mano de obra)
* Extractores de humo − Capture 5 Filtair 400 y extractores de
las series industriales
4. 1 año — Piezas y mano de obra excepto que se especifique
* Sistemas de soldadura AugmentedArc y LiveArc
* Dispositivos automáticos de movimiento
* Pistolas soldadoras MIG Bernard BTB de enfriamiento por
aire (sin mano de obra)
* Unidades sopladoras CoolBelt y CoolBand (no incluye mano
de obra)
* Sistema de secado de aire
* Equipos externos de monitorización y sensores
* Opciones de campo
(NOTA: las opciones de campo [para montaje in situ]
están cubiertas por el tiempo restante de la garantía del
producto en el que están instaladas o por un mínimo
de un año — el que sea mayor.)
* Pedales de control RFCS (excepto RFCS-RJ45)
* Extractores de humo − Filtair 130 y series MWX y SWX
* Unidades de alta frecuencia
* Antorchas para corte por plasma ICE/XT (no incluye mano de
obra)
* Máquinas para calentamiento por inducción, refrigeradores
(NOTA: los registradores digitales están garantizados
separadamente por el fabricante.)
* Bancos de carga
* Antorchas motorizadas (excepto las portacarrete Spoolmate)
* Unidad sopladora PAPR (no incluye mano de obra)
* Posicionadores y controladores
* Racks
* Tren rodante/remolques
* Soldaduras por puntos
* Conjuntos alimentadores de alambre para sistemas Subarc
* Antorchas Tregaskiss (sin mano de obra)
* Antorchas TIG (no incluye mano de obra)
* Sistemas de enfriamiento por agua
* Controles remotos inalámbricos de mano/pie y receptores
* Estaciones de trabajo/Mesas de soldadura (no incluye mano
de obra)
5. Garantía de 6 meses para piezas
* Baterías
6. Garantía de 90 días para piezas
* Juegos de accesorios
* Cubiertas de lona
* Bobinas y mantas para calentamiento por inducción,
cables y controles no electrónicos
* Antorchas M
* Pistolas soldadoras MIG, sopletes de arco sumergido
(SAW) y cabezales externos para soldadura por
recubrimiento
* Controles remotos y control de pie RFCS
−RJ45
* Piezas de repuesto (sin mano de obra)
* Antorchas portacarrete Spoolmate
La garantía limitada True Blue de Miller no tiene validez para los
siguientes elementos:
1. Componentes consumibles como: puntas de contacto,
toberas de corte, contactores, escobillas, relés, tapa de las
mesas de trabajo y cortinas de soldador, o piezas que fallen
debido al desgaste normal. (Excepción: las escobillas y
relés están cubiertos en todos los equipos impulsados por
motor de combustión interna.)
2. Artículos entregados por MILLER pero fabricados por otros,
como motores u otros accesorios. Estos artículos están cubiertos
por la garantía del fabricante, si alguna existe.
3. Equipo que ha sido modificado por cualquier persona que no sea
MILLER o equipo que ha sido instalado inapropiadamente, mal
usado u operado inapropiadamente basado en los estándares
de la industria, o equipo que no ha tenido mantenimiento
razonable y necesario, o equipo que ha sido usado para una
operación fuera de las especificaciones del equipo.
LOS PRODUCTOS DE MILLER ESTÁN DISEÑADOS Y DIRIGIDOS
PARA LA COMPRA Y USO DE USUARIOS
COMERCIALES/INDUSTRIALES Y PERSONAS ENTRENADAS Y
CON EXPERIENCIA EN EL USO Y MANTENIMIENTO DE EQUIPO
DE SOLDADURA.
En el caso de que haya un reclamo de garantía cubierto por esta
garantía, los remedios deben de ser, bajo la opción de MILLER (1)
reparación, o (2) reemplazo o cuando autorizado por MILLER por
escrito en casos apropiados, (3) el costo de reparación y reemplazo
razonable autorizado por una estación de servicio de MILLER o (4)
pago o un crédito por el costo de compra (menos una depreciación
razonable basado en el uso actual) una vez que la mercadería sea
devuelta al riesgo y costo del usuario. La opción de MILLER de reparar
o reemplazar será F.O.B. en la fábrica en Appleton, Wisconsin o F.O.B.
en la sede del servicio autorizado por MILLER y determinada por
MILLER. Por lo tanto, no habrá compensación ni devolución de los
costos de transporte de cualquier tipo.
DE ACUERDO AL MÁXIMO QUE PERMITE LA LEY, LOS REMEDIOS
QUE APARECEN AQUÍ SON LOS ÚNICOS Y EXCLUSIVOS
REMEDIOS, Y EN NINGÚN EVENTO MILLER SERÁ
RESPONSABLE POR DAÑOS DIRECTOS, INDIRECTOS,
ESPECIALES, INCIDENTALES O DE CONSECUENCIA
(INCLUYENDO LA PÉRDIDA DE GANANCIA) YA SEA BASADO EN
CONTRATO, ENTUERTO O CUALQUIERA OTRA TEORÍA LEGAL.
CUALQUIER GARANTÍA EXPRESADA QUE NO APARECE AQUÍ Y
CUALQUIER GARANTÍA IMPLICADA, GARANTÍA O
REPRESENTACIÓN DE RENDIMIENTO, Y CUALQUIER REMEDIO
POR HABER ROTO EL CONTRATO, ENTUERTO O CUALQUIER
OTRA TEORÍA LEGAL, LA CUAL, QUE NO FUERA POR ESTA
PROVISIÓN, PUDIERAN APARECER POR IMPLICACIÓN,
OPERACIÓN DE LA LEY. COSTUMBRE DE COMERCIO O EN EL
CURSO DE HACER UN ARREGLO, INCLUYENDO CUALQUIER
GARANTÍA IMPLICADA DE COMERCIALIZACIÓN, O APTITUD
PARA UN PROPÓSITO PARTICULAR CON RESPECTO A
CUALQUIER Y TODO EL EQUIPO QUE ENTREGA MILLER, ES
EXCLUIDA Y NEGADA POR MILLER.
Algunos estados en Estados Unidos, no permiten imitaciones en cuan
largo una garantía implicada dure, o la exclusión de daños
incidentales, indirectos, especiales o consecuentes, de manera que la
limitación de arriba o exclusión, es posible que no aplique a usted.
Esta garantía da derechos legales específicos, y otros derechos
pueden estar disponibles, pero varían de estado a estado.
En Canadá, la legislación de algunas provincias permite que hayan
ciertas garantías adicionales o remedios que no han sido indicados
aquí y al punto de no poder ser descartados, es posible que las
limitaciones y exclusiones que aparecen arriba, no apliquen. Esta
garantía limitada da derechos legales específicos pero otros derechos
pueden estar disponibles y estos pueden variar de provincia a
provincia.
El original de esta garantía fue redactado en términos legales
ingleses. Ante cualesquiera quejas o desacuerdos, prevalecerá el
significado de las palabras en inglés.
¿Preguntas sobre la
garantía?
Llame
1-800-4-A-MILLER
para encontrar su
distribuidor local de
Miller (EE.UU. y
Canada solamente)
miller
warr
spa 2017−01